For the last two years, Knorr-Bremse’s Berlin-based subsidiary Hasse & Wrede has been using robots to support employees involved in manufacturing viscous torsional vibration dampers. Managing Director Markus Mali talks about the reasons for automation, the positive consequences for the workforce, and the future opportunities offered by Industry 4.0.
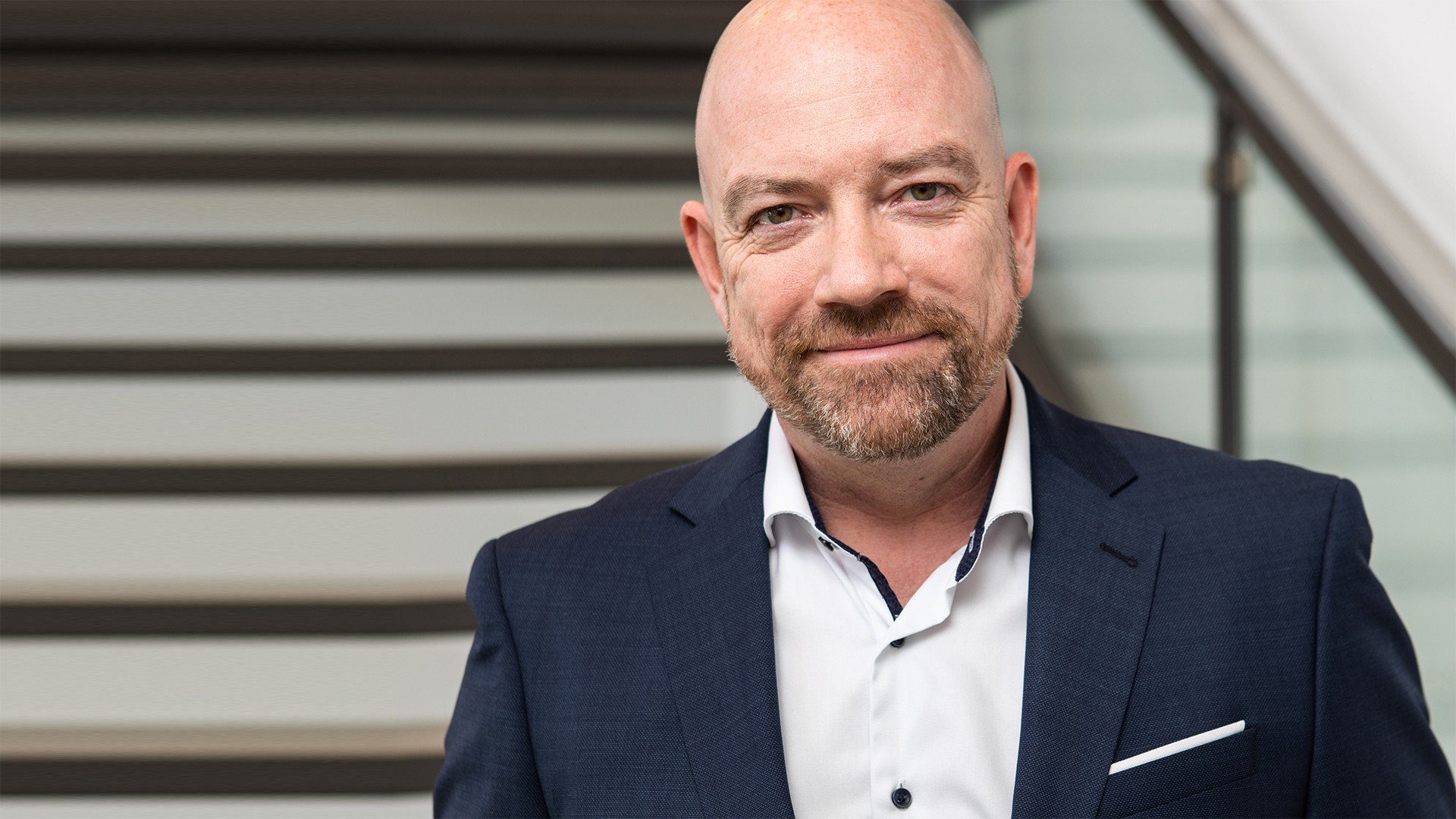
Mr. Mali, Hasse & Wrede manufactures torsional vibration dampers – what are they, and why do people need this (rather unusual) product in the first place?
It’s true, very few people know much about our products. And yet you’ll find torsional vibration dampers in many millions of drivetrains worldwide. By reducing the torsional vibrations generated along the crankshaft, they ensure that engines keep running safely and reliably. In terms of both technology and market share, Hasse & Wrede is a world leader in torsional vibration dampers. About half of our business consists of dampers for what are generally known as “on-highway” applications, meaning engines for commercial vehicles and passenger cars. The other half of our business consists of dampers for “off-highway” and industrial applications, meaning anything that doesn’t run on roads. This includes, for example, power generation equipment, construction and agricultural vehicles, but also ships.
With respect to ships, one of the most prominent examples is the “Polarstern” (Polar Star) used by the German expedition to the South Pole. Tell us a little more about it.
Toward the end of 2020, Hasse & Wrede completely overhauled two of the four viscous torsional vibration dampers installed in the engines of the “FS Polarstern” – obviously the ship’s propulsion system had to be able to withstand the extreme conditions in Antarctica. To ensure it would be able to do so, we spent two weeks servicing both dampers in our Berlin plant. This commission gave us enormous pleasure, but was also a very special honor. (magazine article: "Extreme logistics in the eternal ice" )
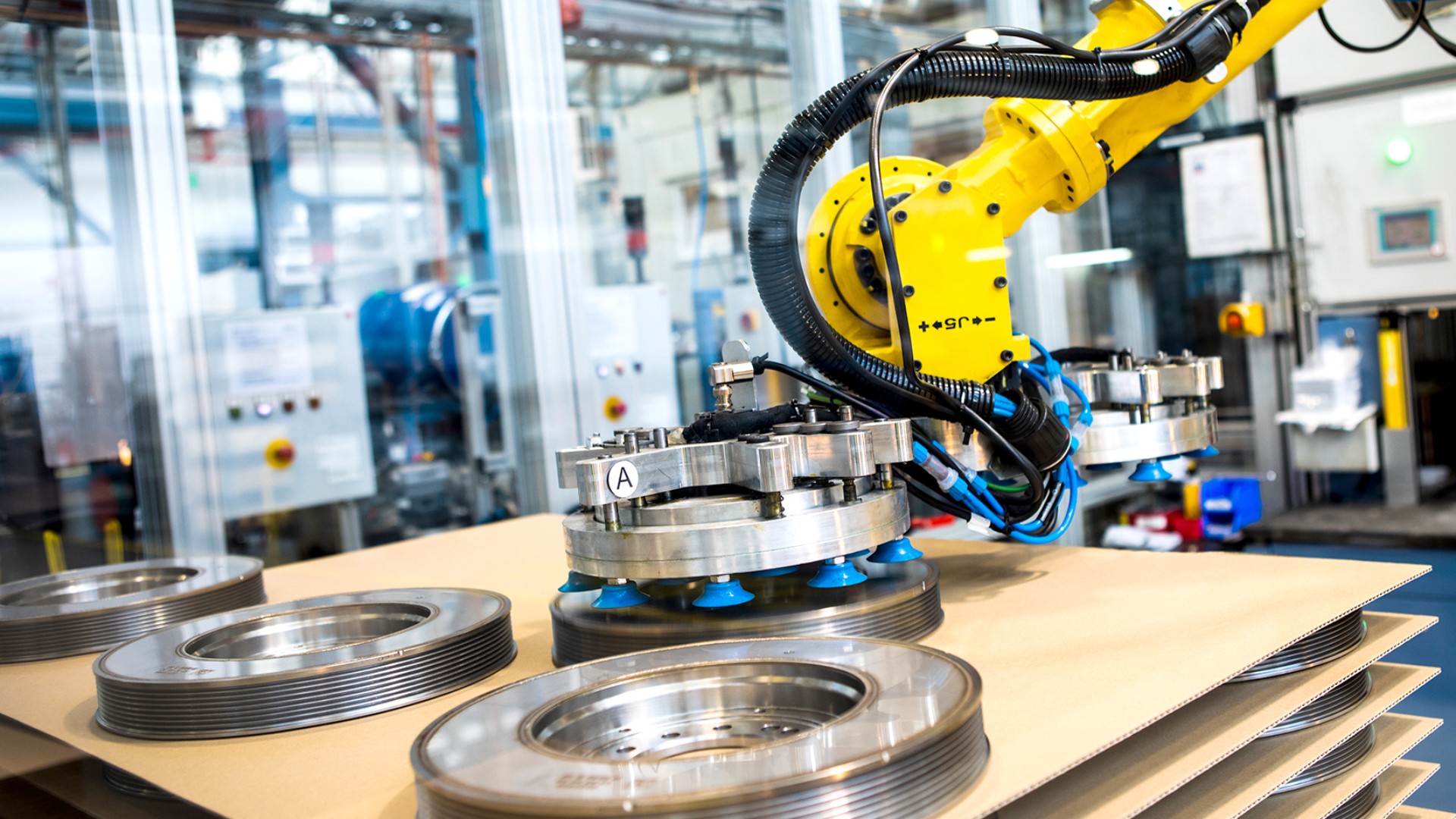
What’s the overall business situation at Hasse & Wrede?
Despite all the downsides, we’ve successfully weathered the period since the outbreak of the pandemic, benefiting in particular from the stability of the off-highway market. Our business is still doing very well right now – our order books are full, and orders have gone back up to the levels they were at before the COVID-19 crisis. We’d have even more to do if our truck-manufacturing customers were able to get hold of enough microcontrollers for their vehicles. But because of the ongoing global chip crisis, semiconductors are still in short supply. I’m glad to say that worldwide demand for our vibration dampers is as high as ever.
What particular issue is taking up most of your attention right at this moment?
Clearly it’s got to be the partial automation of our manufacturing operations in Berlin. Just now, that’s one of our core strategic priorities. We’ve been able to tackle this ambitious project because back in 2017, Knorr-Bremse Commercial Vehicle Systems (CVS) decided to maintain and modernize our Berlin site. For me this was – indeed, still is – an important indication that even in a country like Germany, competitive industrial manufacturing will still be possible in the future if we simultaneously invest in the necessary automation and digitalization of our plants and systems. And that’s the kind of investment project we’ve been given the chance to implement here in Berlin.
So what have you modernized or automated at Hasse & Wrede in Berlin?
We’re in the process of building partially automated production cells. Each of these cells is a separate, enclosed space in which an industrial robot feeds workpieces into and out of the various machines arranged around it. The integrated machines handle the production process that produces the finished dampers. This means that they’re welded, tested for leaks and smooth operation, then filled with silicone oil and palletized. Human beings continue to work in each of these cells – as well as setting up and supervising the cell, they’re also responsible for assembling, labelling and sealing the dampers, and carrying out visual inspections. Our first production cell kicked off its series production activity in early 2020 and is now producing up to 300 dampers per shift. We’re currently running two of these cells in Berlin, with a third under construction.
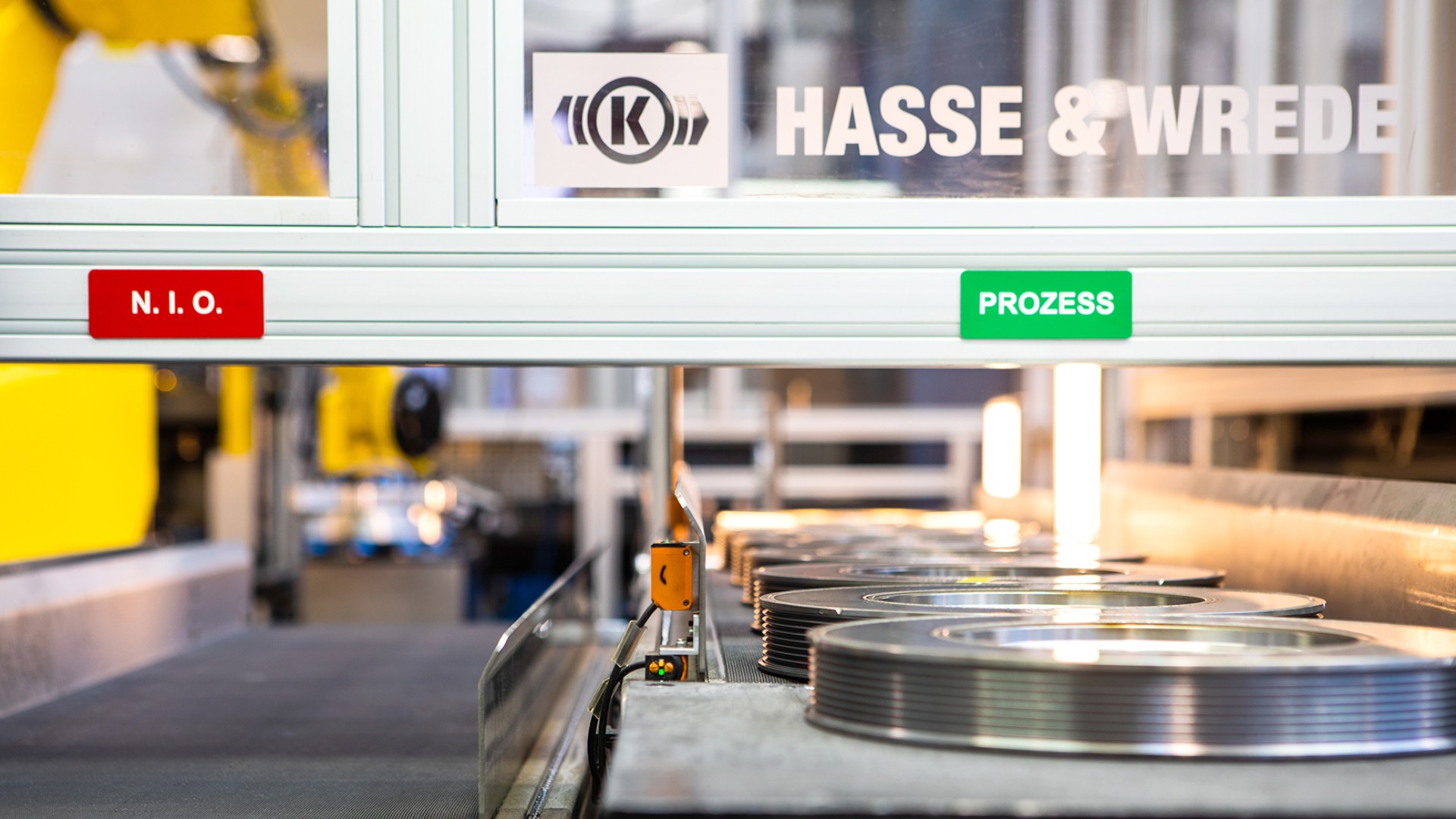
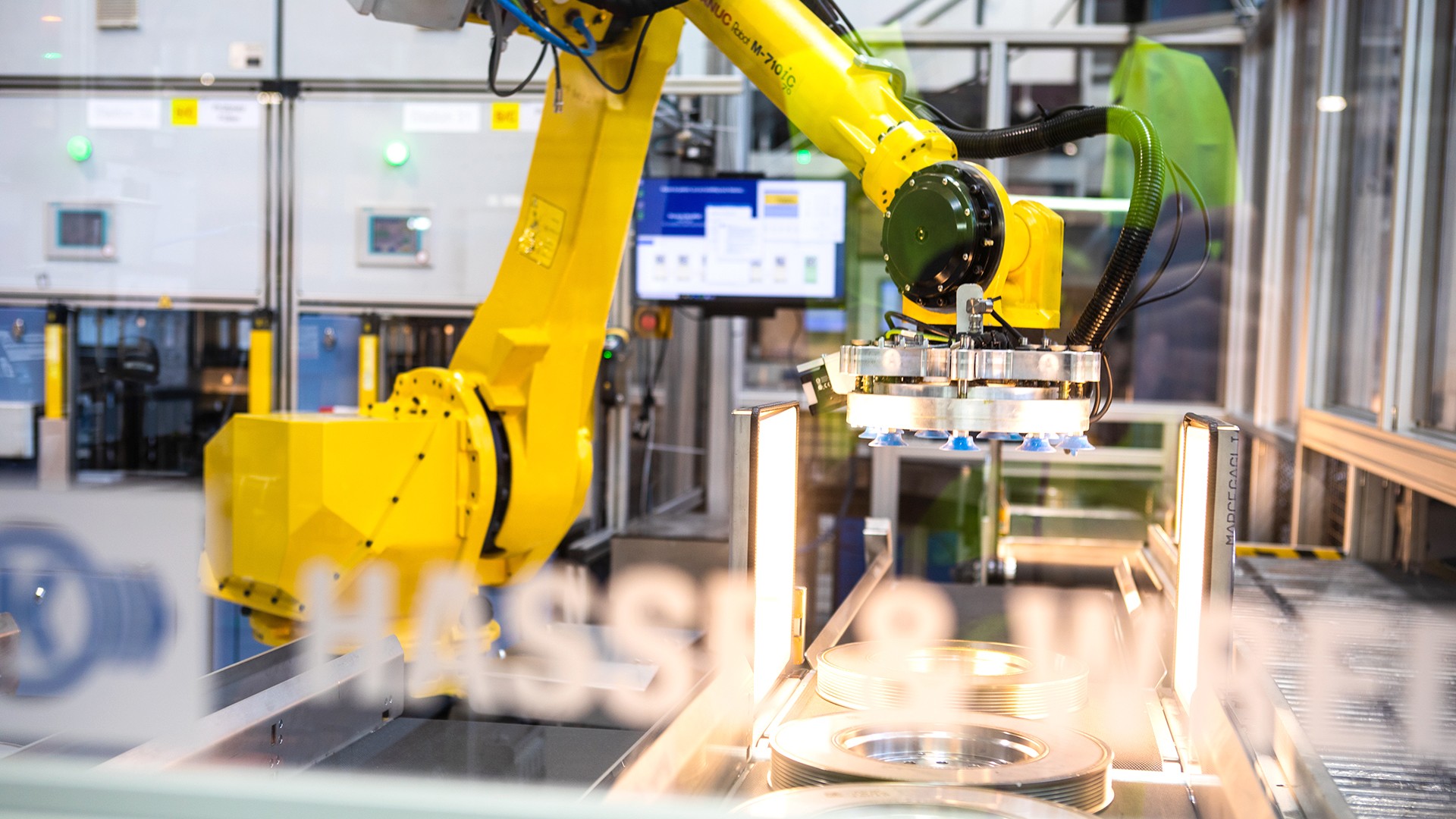

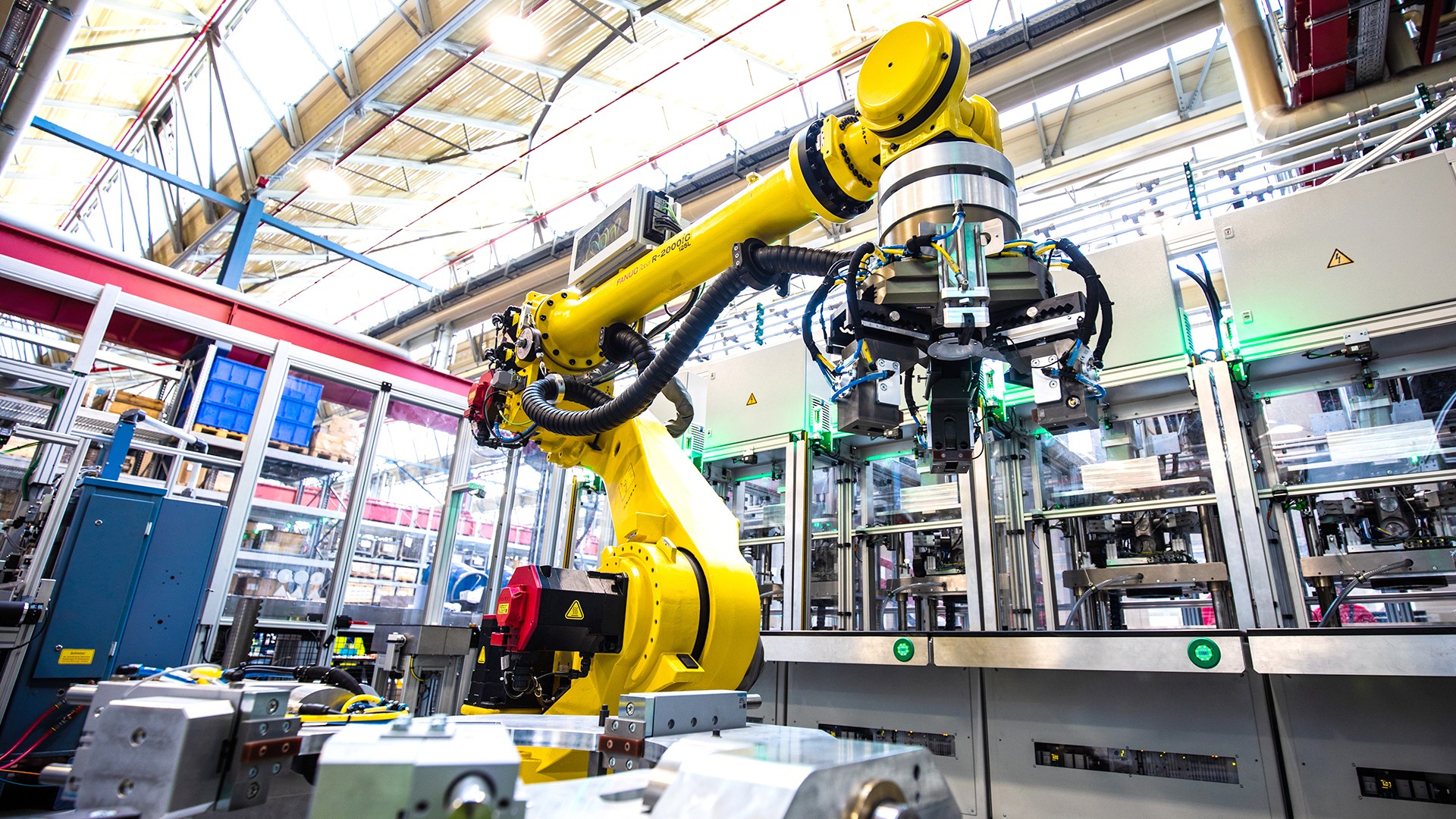
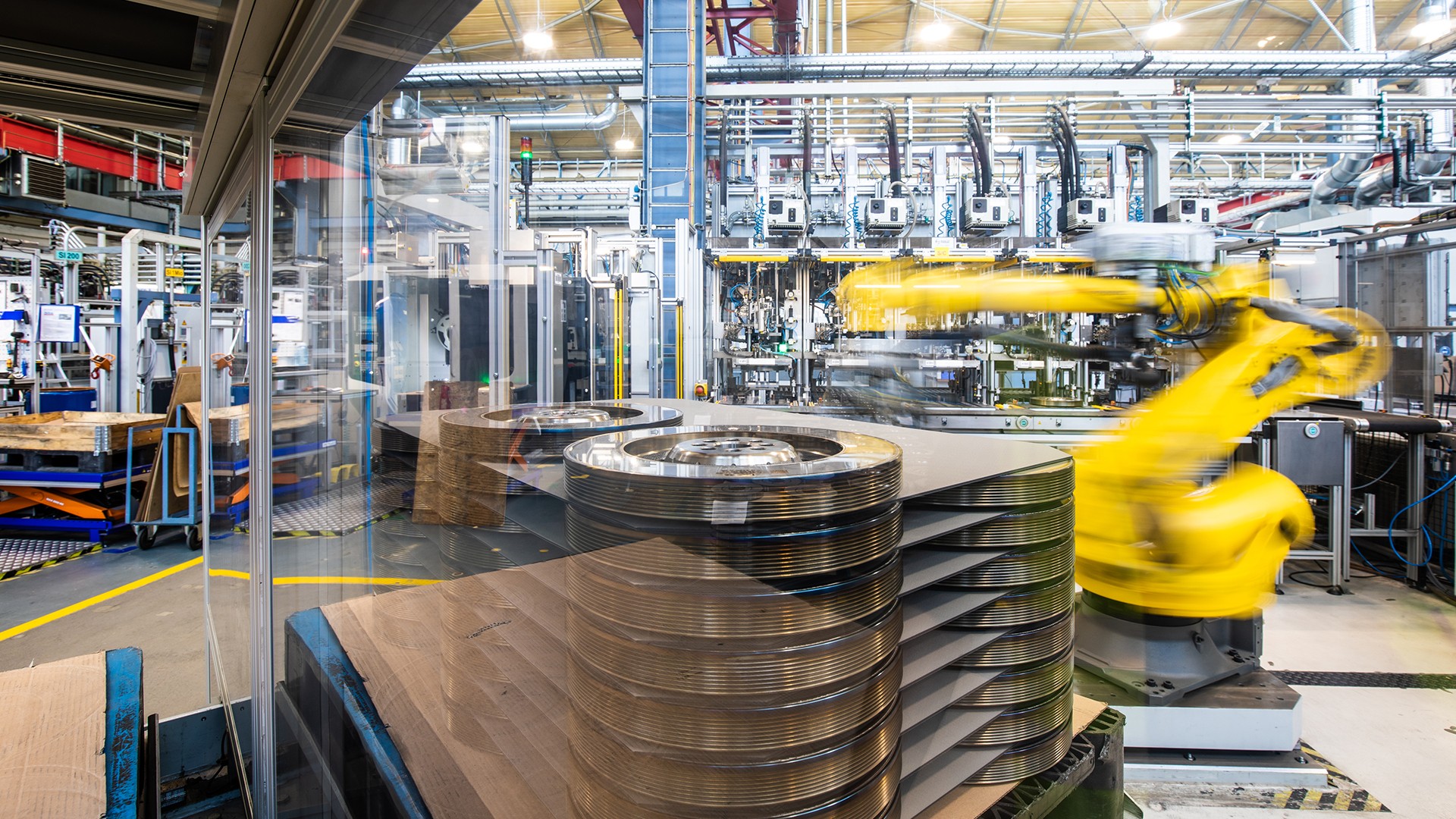
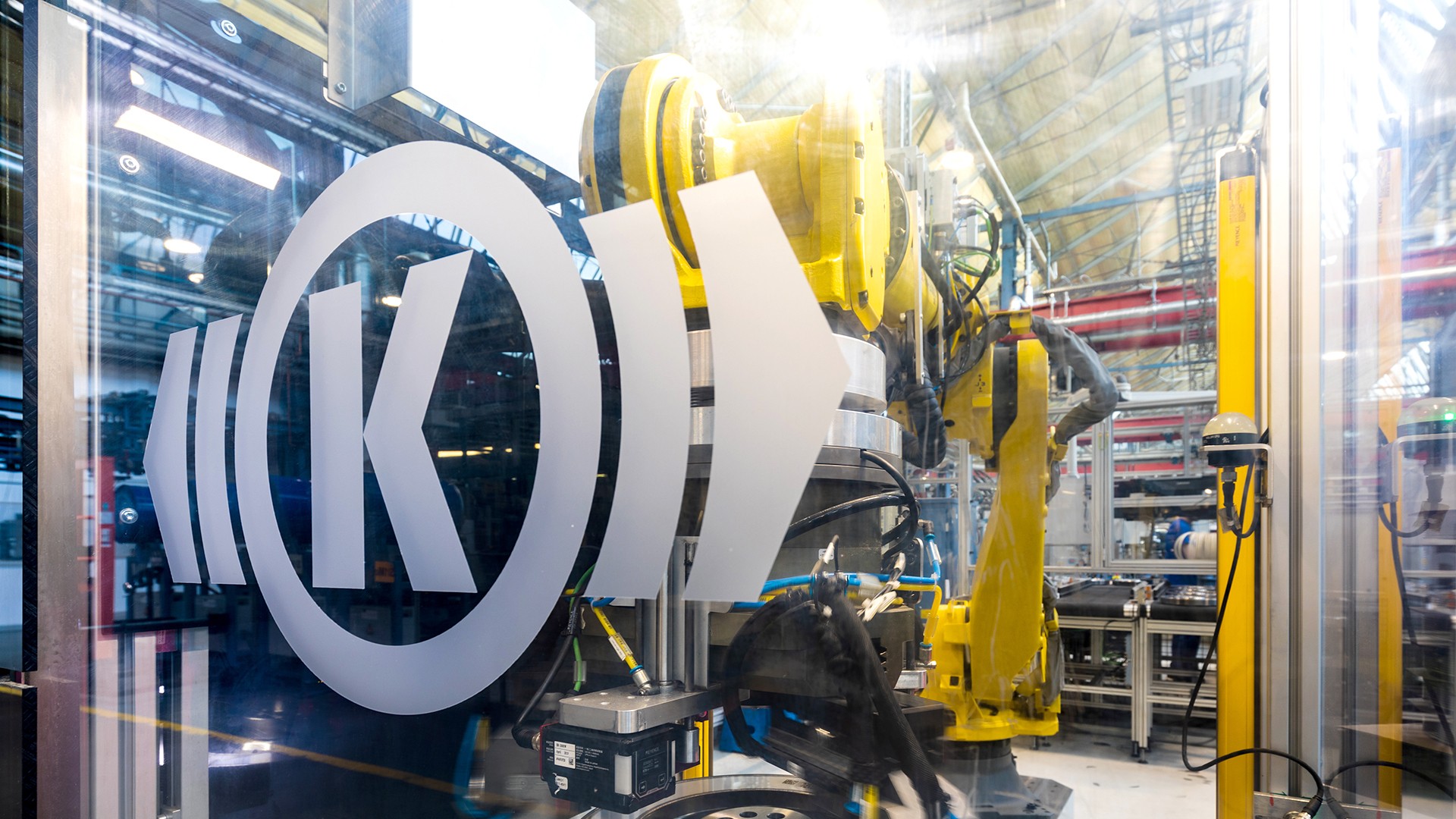
What does this automation mean for your production teams?
The new robots take over laborious manual processes, improving workplace ergonomics and making people’s working lives easier. The number of heavy loads our employees must lift and carry around has plummeted. What’s more, the robots reduce production hazards and sources of risk. While the robot is working in its cell, nobody is allowed in there – an employee feeds and controls the process from a workstation outside the cell. That’s a huge improvement over the previous situation; until recently, up to three employees working on a comparable manual production line had to do all the physically strenuous work that’s now being done by machine. Overall, automation is also bringing us considerable safety, cost and quality benefits.
Does this mean Hasse & Wrede will soon be using machines throughout the core manufacturing operation?
No. We’ll continue to use employees in many areas of production, for a number of very good reasons. First, they still do a better job in these areas than any machine – when assembling components, for example, or inspecting the welded dampers. No system is as good at reliably and precisely detecting even the tiniest welding defects as our experienced employees – and that’s in addition to the technical inspections we carry out in any case. In short, I’m quite sure that human beings are still indispensable in today’s industrial world and will continue to play a key role in production and manufacturing.
How are people’s jobs changing in production as a result of increasing automation?
While the work is less physically demanding, in other ways it’s become more challenging. We need more and more production staff who are capable of controlling and monitoring machines and rectifying minor defects themselves. We also need what are known as process technicians and engineers – specially trained production employees who take responsibility for specific operational processes. This is opening up new opportunities for anybody who wants to upgrade their skills at our Berlin plant. We’re helping our employees to qualify for new jobs while simultaneously stepping up our training and vocational development program.
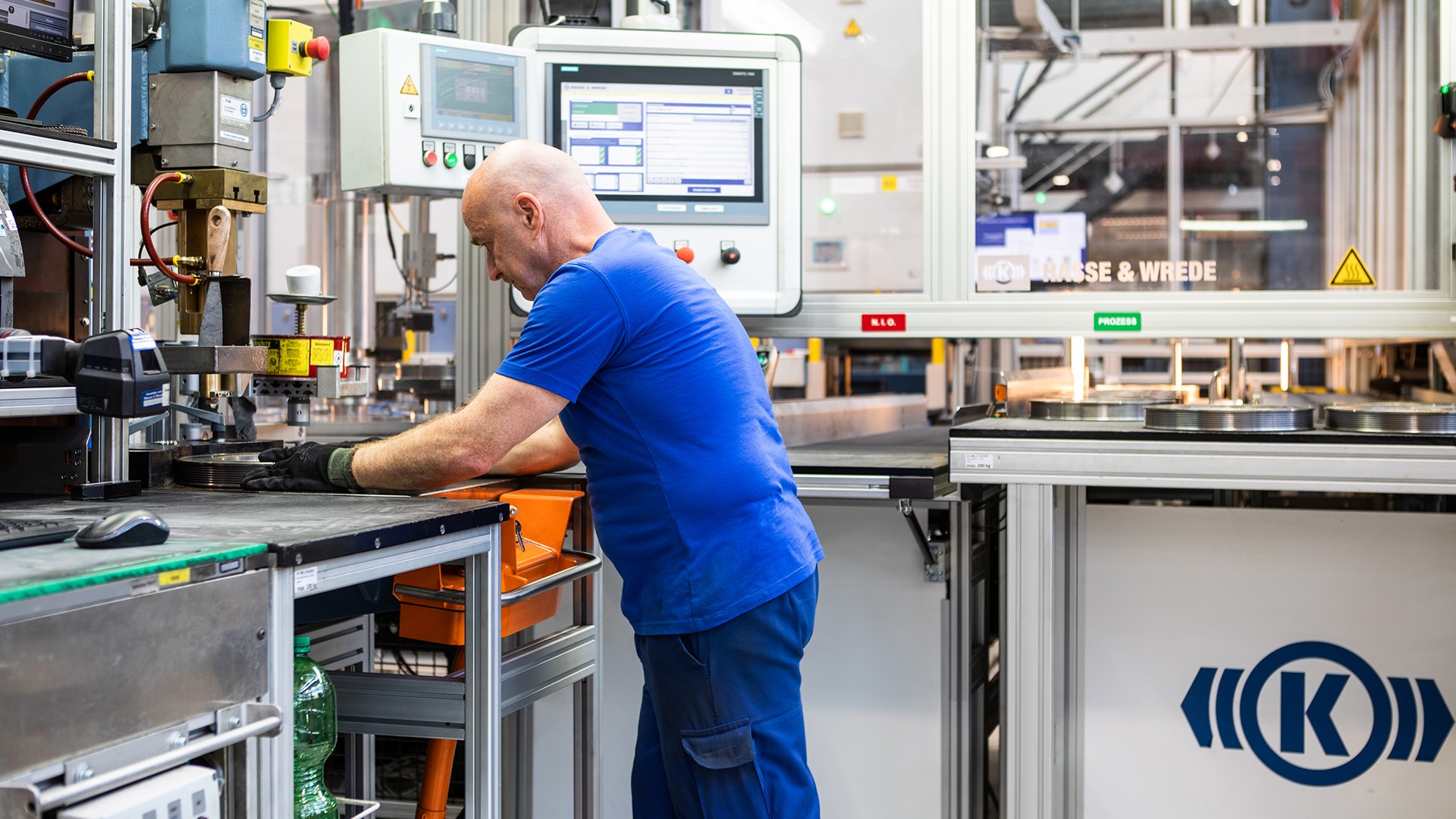
How difficult was it for a traditional manufacturer like Hasse & Wrede to implement these automation initiatives?
It was a huge challenge for our company. Hasse & Wrede comes from a manufacturing tradition characterized by manual, mechanical, non-digital production. But we took the decision to start transforming our production operation into a substantially more automated one at just the right moment. With our new production cells, we’re the first company in our industry, anywhere in the world, to manufacture torsional vibration dampers with this level of automation. That’s helping us to secure a sustainable future for our Berlin site, consolidate our market-leading expertise, and remain competitive in the long term. Of course we had to start by acquiring the technical expertise to implement this automation, but we were able to rely on plenty of support from our parent company.
“Industry 4.0” is a major issue for all manufacturing companies. In the future, factories will be capable of pretty much organizing themselves, and machines will communicate with each other. How would you define the level of automation at Hasse & Wrede in this context?
For Hasse & Wrede, our efforts to become more automated represent a major step toward “Industry 4.0”. As part of this initiative, we’ve also started to network our production machines and integrate them into a single production control system. We’re using PTC ThingWorx to do this – an IoT (Internet of Things) platform that’s currently being rolled out in multiple pilot projects across the company, with support from CVS’s central Industrial Engineering team. All this will make it possible for us to gain more and better insights into our production workflows and process parameters in the future, so we can further optimize them and reduce undesirable downtime. In this respect, our Berlin plant is acting as the Knorr-Bremse Group’s pioneering manufacturer of torsional vibration dampers. And this, of course, is something that will also benefit our production facilities in Asia, as well as North and South America.
Hasse & Wrede
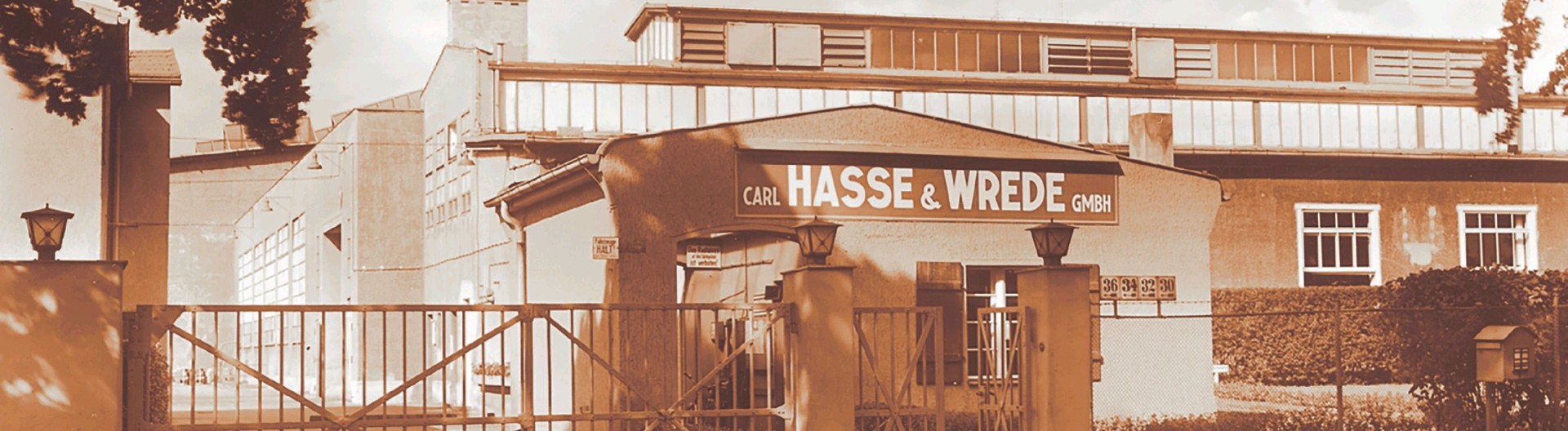
Hasse & Wrede celebrates 125th anniversary in 2022
- Hasse & Wrede develops, produces and sells viscous torsional vibration dampers (or “viscous dampers” for short) for commercial vehicles, passenger cars, ships and industrial applications.
- The company manufactures its products in Berlin and at sites in North and South America and Asia.
- The total number of employees working in Berlin is around 180
- Long-established manufacturing firm Hasse & Wrede was founded in 1897 by Carl Hasse and Julius Wrede, and has championed innovation and advanced technology for the past 125 years.
- Hasse & Wrede has been part of the Knorr-Bremse Group since 1921 – so the company has been a Knorr-Bremse subsidiary for over a century.