With augmented reality (AR), Knorr-Bremse is taking one of the next steps on the road to digital transformation. Climate-friendly technology that also enables Covid compliance.
It has now become so commonplace to hold video conferences via Teams, even in the office, that people hardly remember how they used to conduct meetings, especially for teams spread out over several locations. Many weekly meetings start with a laugh over a new video background, mechanics in the workshop simply turn their mobile phone around during the video call to show the expert at the hotline PC a live image of what is currently raising questions on site. Florian Amann, Technology Team Lead at Knorr-Bremse Commercial Vehicle Systems in the unit headed by Thorsten Dankwort (T/R-IE): “This is standard today. Now, with augmented reality, we can take the next step.”
More than a mobile video conference
“In fact, the AR system can do far more than just make video conferencing mobile,” explains Korbinian Paul, an expert in digitalization technologies. “At its core, an AR system consists of a conferencing platform and more or less sophisticated smart glasses. It offers a user interface for the conferencing system via voice control, delivers audio via headphones and shows the conference participants what the user is currently seeing in their location via an integrated video camera. Meanwhile, they have both hands free to directly perform even complex tasks.”
In contrast to a virtual reality (VR) system, which shows the viewer an exclusively digital environment, the AR glasses provide a clear view of the actual objects present and can additionally overlay documents or graphics via a display. “Reality, enhanced by supplementary information, all in one field of vision, with the extra option of simultaneously consulting with colleagues – that opens up a lot of new possibilities,” says Paul.
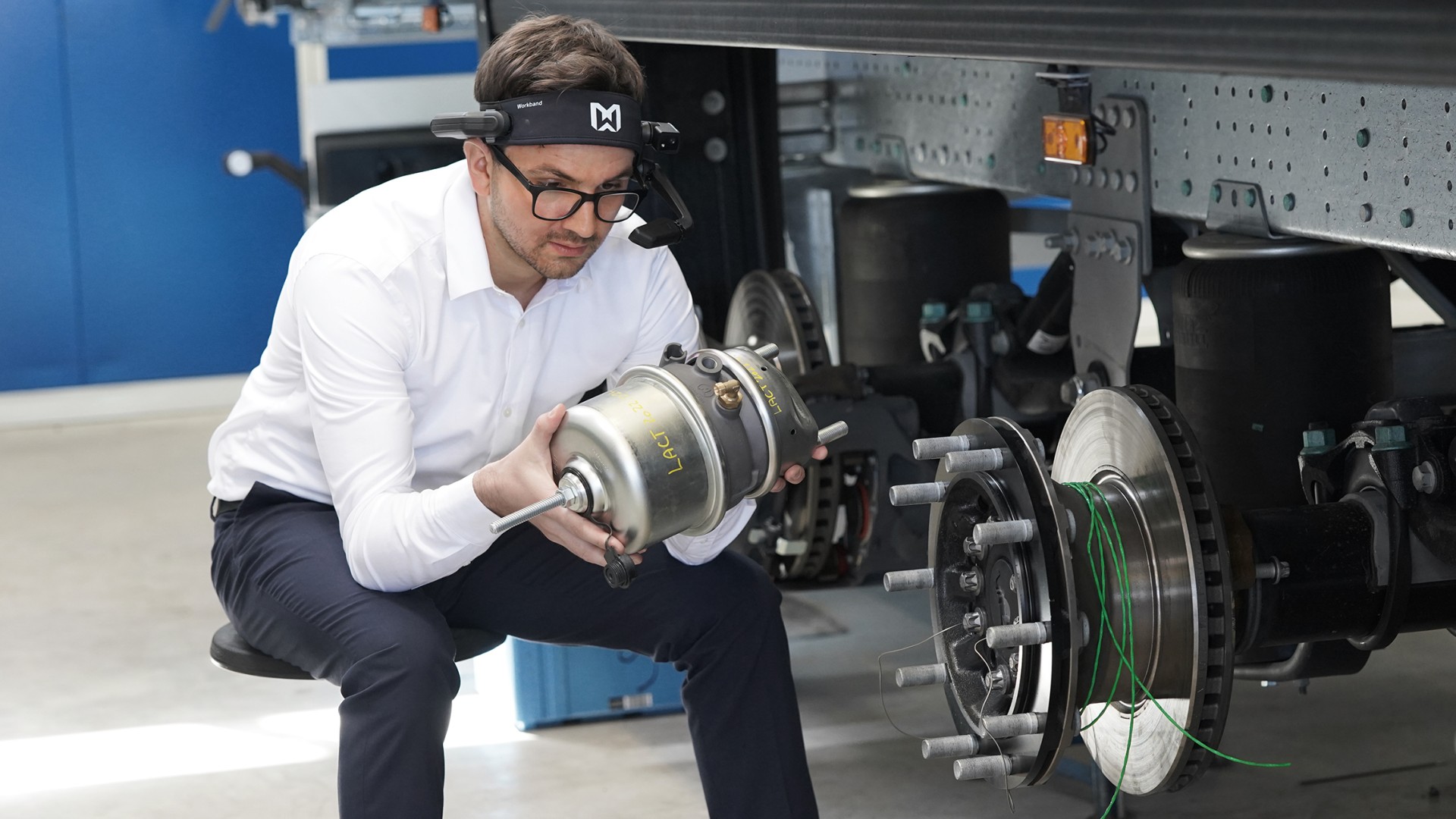
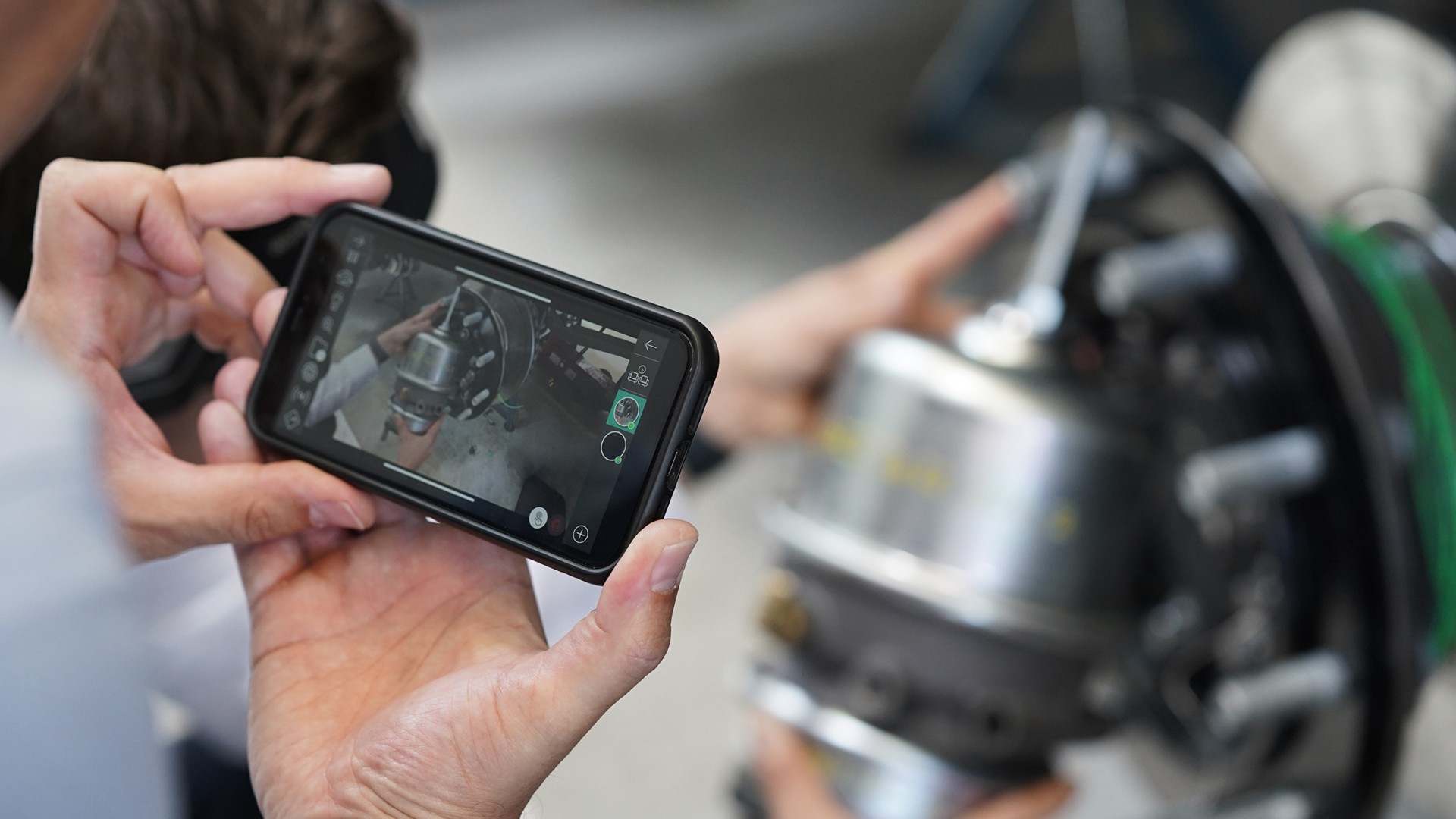
Assistance is on hand: next generation training or service
Anyone sitting at a screen with a question about software they are using can call the hotline and share their screen. But what to do when the issue is not in the digital realm, but out there in the real world? Mechatronics engineers who have a question in a truck workshop, test run results that need to be discussed among a group of experts, customer personnel who encounter new issues when installing a braking system, or perhaps the on-site training of engineers when a new production line is being set up. In situations like these, the AR glasses and platform can be used to get assistance – or to make the conference the subject of discussion. “AR essentially opens up a whole host of development opportunities,” says Amann. “In theory, we can have AR glasses fill a production hall, which may still be completely empty in real life, with graphics of the machines to be set up, and allow the personnel on site to assemble them part by part.” But as a first step, he says, the enhanced conferencing capabilities of an AR system are the most compelling. It will still be important to get fitters, technicians or engineers together for training, or to directly share problems in production with colleagues in the office, at other sites or with suppliers. Amann adds that AR could be an additional tool of choice for this next generation of service or coaching on the product.
Forming new habits
AR platform providers have been evaluated, and Amann and his team have also tested various end devices. Those who want to gain first-hand experience with the capabilities of the technology in their own area of the company have the opportunity to participate in trials within a pilot project. According to Amann, “The effort required to use this technology is extremely low.” Often, the main task is to discard previous habits and establish new processes.

Practice makes perfect
Not everything about an AR system is self-explanatory. The voice control for the function menu, for example, takes some getting used to. “As with anything, practice makes perfect,” says Amann with a smile. “But anyone who has already used Alexa to order a pizza or activated Google search on their new smartphone via voice control has already cleared the biggest hurdle.”
Info
Premysl Jezek, Testing Engineer TruckServices at the Reman plant in Liberec
At one of the peaks of the Covid-19 pandemic, a new Universal Test Bench was to be installed at the Knorr-Bremse plant in Liberec, Czech Republic. “As a rule, the relevant experts travel to the site for this purpose to carry out the installation and training,” says Premysl Jezek, Testing Engineer TruckServices at the Reman plant in Liberec. At that time, however, this was not possible due to the entry restrictions in place. It was uncertain when the regulations would change again. “The AR system served us extremely well during this time,” says Jezek. He made one or two test runs with the voice control among his colleagues, then he was ready to conduct the coaching sessions on the Universal Test Bench. In his ear were the experts who were working from home, each of them seeing exactly what Jezek was seeing. There was no need to train the voice recognition of the AR system, nor did Jezek have to keep the command manual for the control system next to him. Jezek: “There was no need for complicated explanations of connecting cables or sockets. The colleagues were precisely informed every step of the way and were able to provide support precisely where it was needed.”