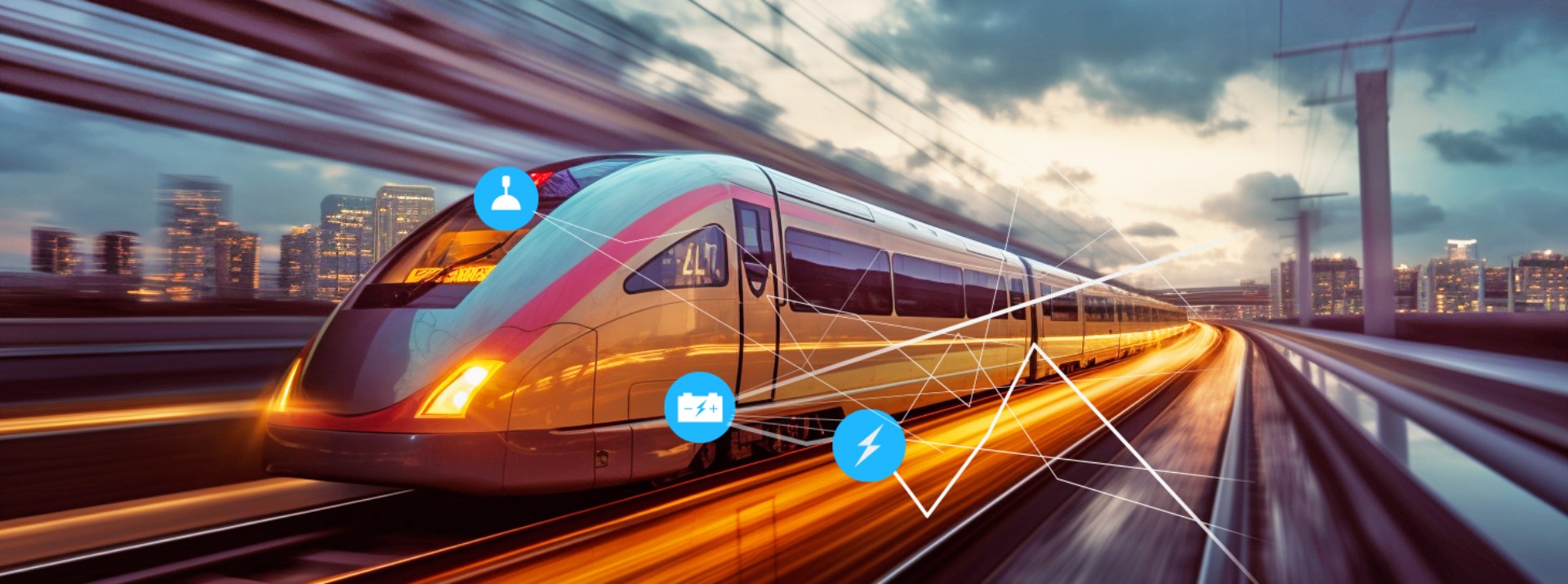
In the future, sustainable mobility will depend in large part on rail transportation – a vision which Knorr-Bremse is helping to deliver by designing innovative technologies. With the Electromechanical Train Braking System (EM brake), the world market leader is currently working to bring about a technological revolution. Just why the EM braking system will play such a pioneering role in the train of the future, and why pneumatic brakes will continue to play a vital role for a long while yet, are among the questions addressed in this interview by Knorr-Bremse’s Matthäus Englbrecht, Vice President Global Brake Systems, and Josef Baier, Director Brake Domain Systems.
Let’s start with a quick retrospective: In the early days of rail, human “brakemen” were responsible for manually braking train cars. Then, toward the end of the 19th century, the pneumatic brake appeared and quickly spread around the world. Pneumatic brakes are controlled by a complex system that uses compressed air to press the brake pads onto the brake discs – a system that has steadily evolved to become today’s standard. So would it be reasonable to say that the electromechanical brake is about to open the next big chapter in the development of train braking systems?
Matthäus Englbrecht: To be absolutely precise, today’s state of the art is the electropneumatic brake, a major evolutionary step beyond pure compressed air. This means that the pneumatic system in modern trains is supported by sophisticated mechatronics and software. More or less all the major lines of development in the transportation industry are heading in the direction of electrification, connectivity and eco-efficiency. So abandoning pneumatic systems and going all-electric does indeed represent a new chapter – a genuine paradigm shift.
The electropneumatic braking system has been continuously developed over many decades, proving its worth in millions of trains run by rail operators around the world. So why is this the right moment to introduce a brand-new technology?
Matthäus Englbrecht: Innovations are driven primarily by the needs of train manufacturers and rail operators. And increasingly, they’re looking for vehicles that run even more efficiently, save energy, and weigh less. Similarly, they’re anxious to streamline the flow of traffic. To make better use of the rail network and move more people from A to B, trains need to run more often, at shorter intervals. Cutting maintenance costs is another major concern. In view of these needs and demands, it makes sense to consider how we can best contribute – for example by providing new technologies for brakes, one of the most complex train systems.
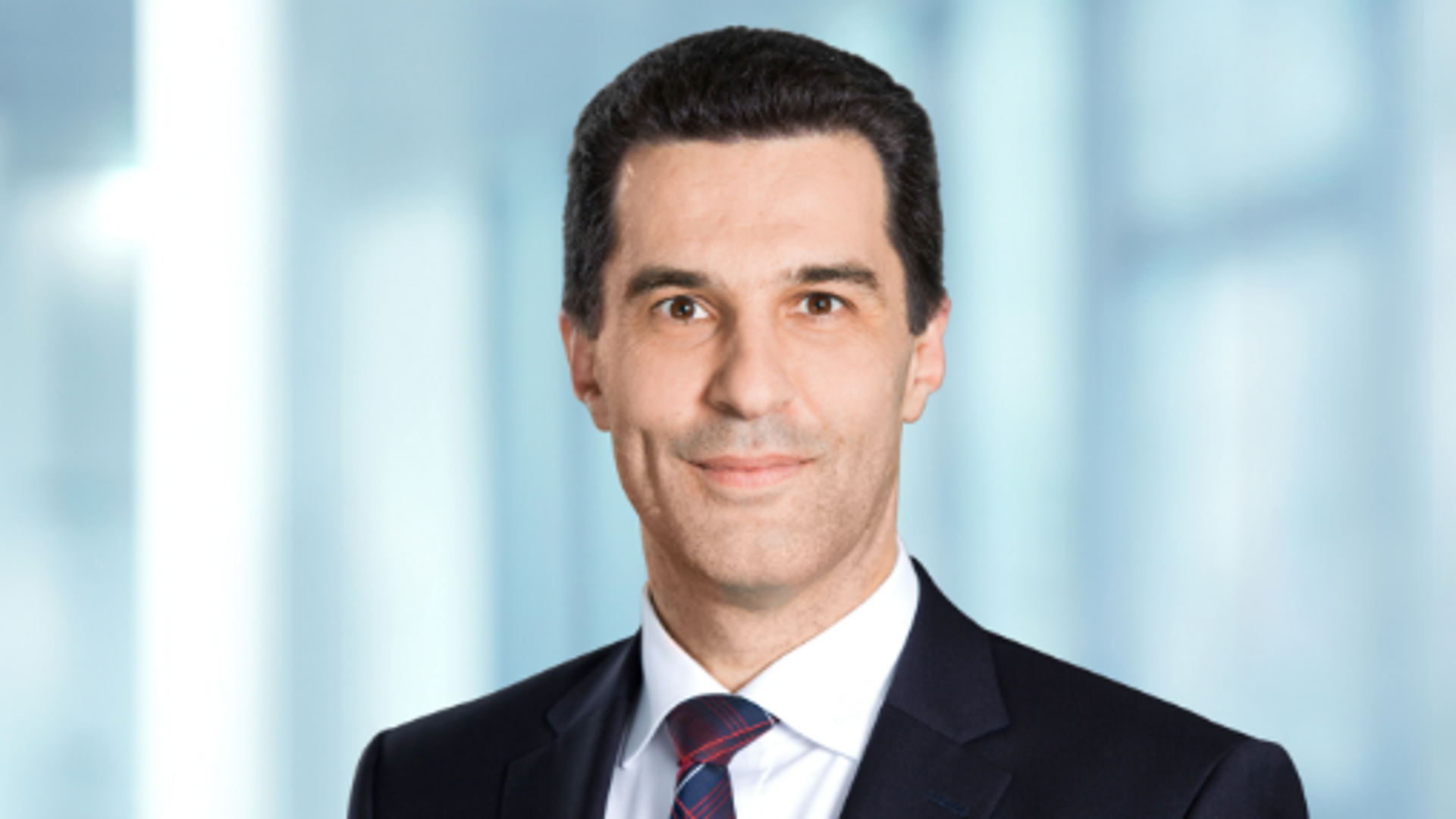
Josef Baier: Today’s electropneumatic brake is a very mature, highly reliable system. But the only way to satisfy many of the criteria we’re discussing is to make a major technological leap forward. Another good reason for such a leap is that we now have electric motors and other components that are capable of withstanding rigorous operating conditions involving shocks and vibrations, and can be mounted in the actual brake calipers.
So here’s the question: Will the electromechanical brake replace the pneumatic brake?
Matthäus Englbrecht: No. The electropneumatic brake will continue to exist in parallel with the electromechanical brake. It will continue to form the backbone of the braking technologies used in trains for a long while yet – and remain a highly relevant market for us. The EM braking system is another advanced technology with many new features, such as electrification and connectivity; it represents an alternative to pneumatic systems. Initially, we expect it to be used in specific areas of application, where it will help to overcome the challenges currently facing the rail industry. As an alternative system, it will continue to evolve in significant ways for decades to come.
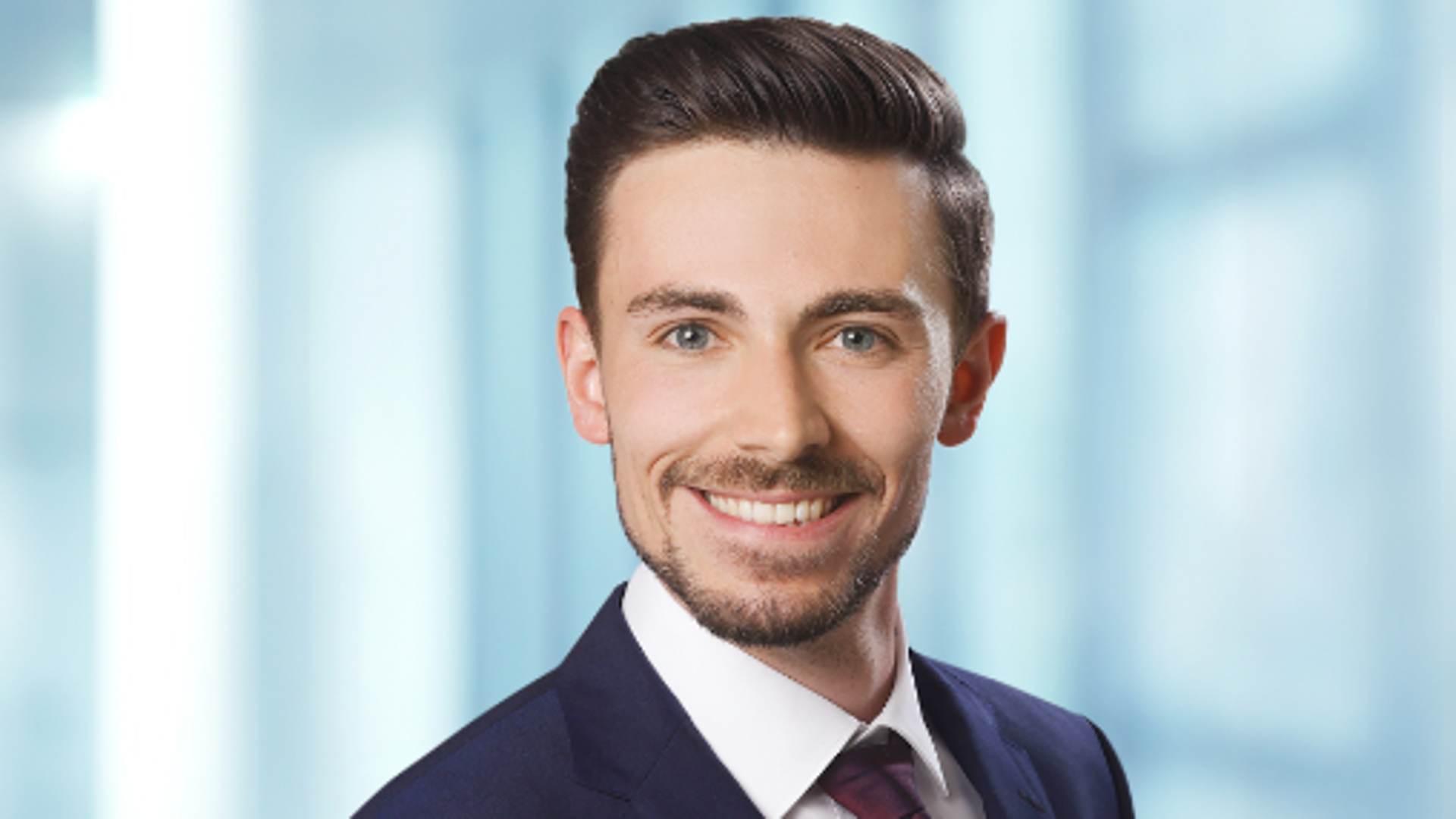
As soon as the EM braking system is market-ready: Where can we expect to see it in the first instance?
Matthäus Englbrecht: We believe that EM brakes will initially appear in light rail vehicles, including trams and streetcars, but also in mainline trains – especially metro, regional and high-speed trains. The architecture of these vehicles already meets almost all the requirements for installing an EM braking system. Unlike vehicles that are regularly coupled and uncoupled, such as locomotives, passenger cars or freight cars, the power supply is electric throughout. And you need electrical signal transmission to install an EM braking system, because everything that’s currently done with valves and pipework is replaced by electromechanical technology. Braking signals are transmitted by a “brake-by-wire” system – that is, electrically, via cables – instead of compressed air or hydraulic fluid.
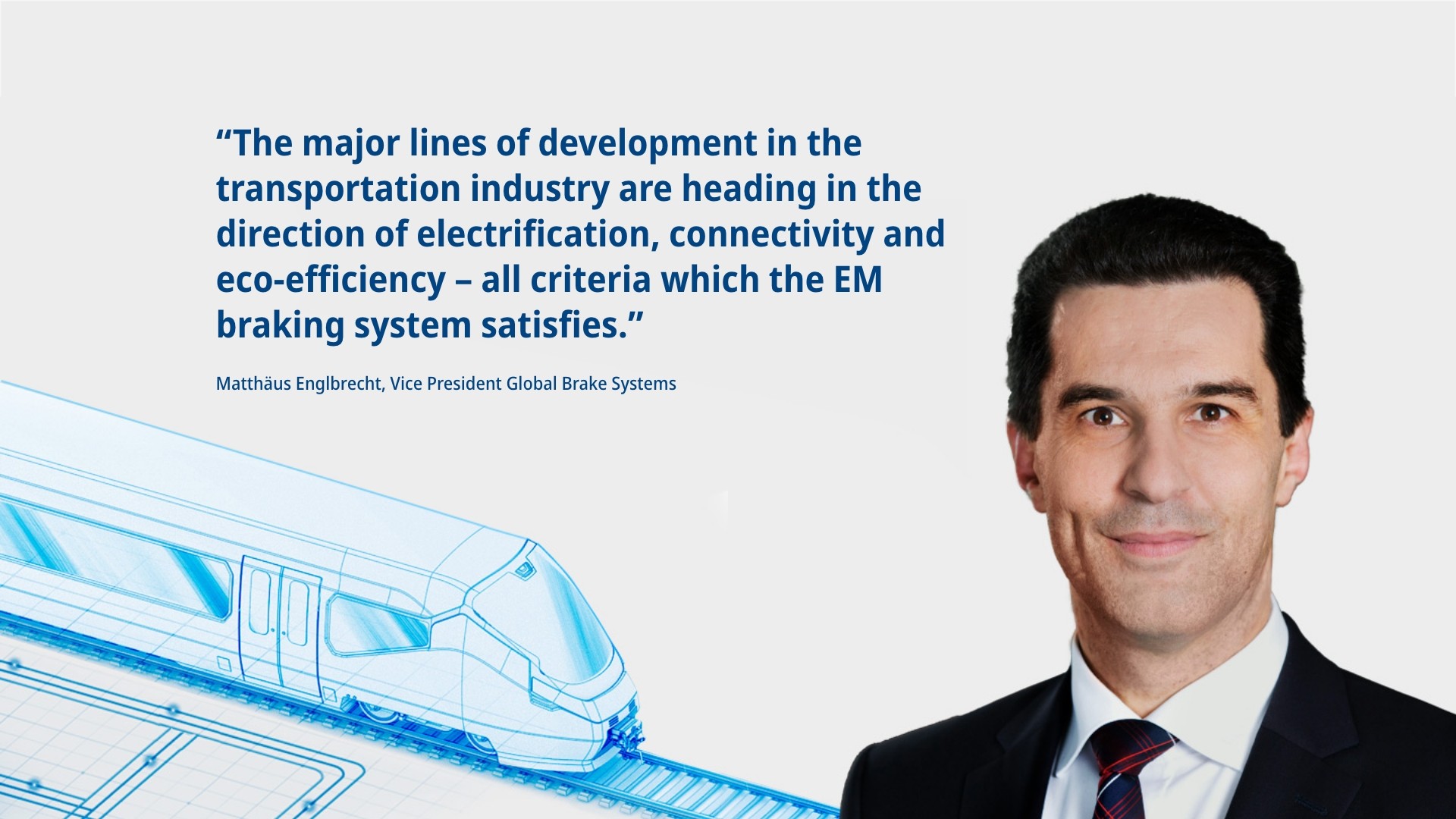
Let’s talk about the immediate benefits of the EM brake. What do train operators and transit companies get out of investing in the EM braking system?
Josef Baier: Because it’s equipped with sensor systems and networked with other train systems as well as the Cloud, the EM braking system will make it easier to check and test components so that maintenance cycles, for instance, can be optimized. Predictive maintenance can save operators time and money. Another advantage is the potential for reducing braking distances, because EM brakes transfer braking force even faster and can be controlled even more precisely. That’s why an EM braking system is even better at preventing wheel slide in difficult track conditions than today’s purely pneumatic wheel slide protection systems. What’s more, EM brakes are more efficient – and that also means more energy-efficient – than pneumatic braking systems, which must compress air in a compressor so they can use it as the medium for transmitting braking signals. Inevitably some of the energy used to do this is converted into heat energy and lost, whereas in an EM braking system, almost all of the input energy is directly applied to the brakes.
And what about weight reduction?
Josef Baier: The actual braking system alone can weigh as much as 15 percent less, depending on how the vehicle is configured. And that’s before you take all the pneumatic pipework into account, which you no longer need if you have electromechanical brakes. It’s a simple equation: When trains have less weight to carry around, they need less traction energy.
Relatively speaking, electromechanical brakes are very space-efficient because they don’t need compressed air lines or tanks. Leaving more room for other train components such as climate control systems and electronics. But another, equally compact system is currently available – the electrohydraulic braking system used in light rail vehicles, i.e. trams. So why do we need electromechanical brakes?
Josef Baier: Electrohydraulic systems use oil as the fluid medium for transferring power. As a medium, the compressed air used in pneumatic systems isn’t problematic, whereas oil can be. For example, handling oil in workshops is a laborious business. Knorr-Bremse’s electromechanical braking system doesn’t need any extra oil at all to use as a medium.
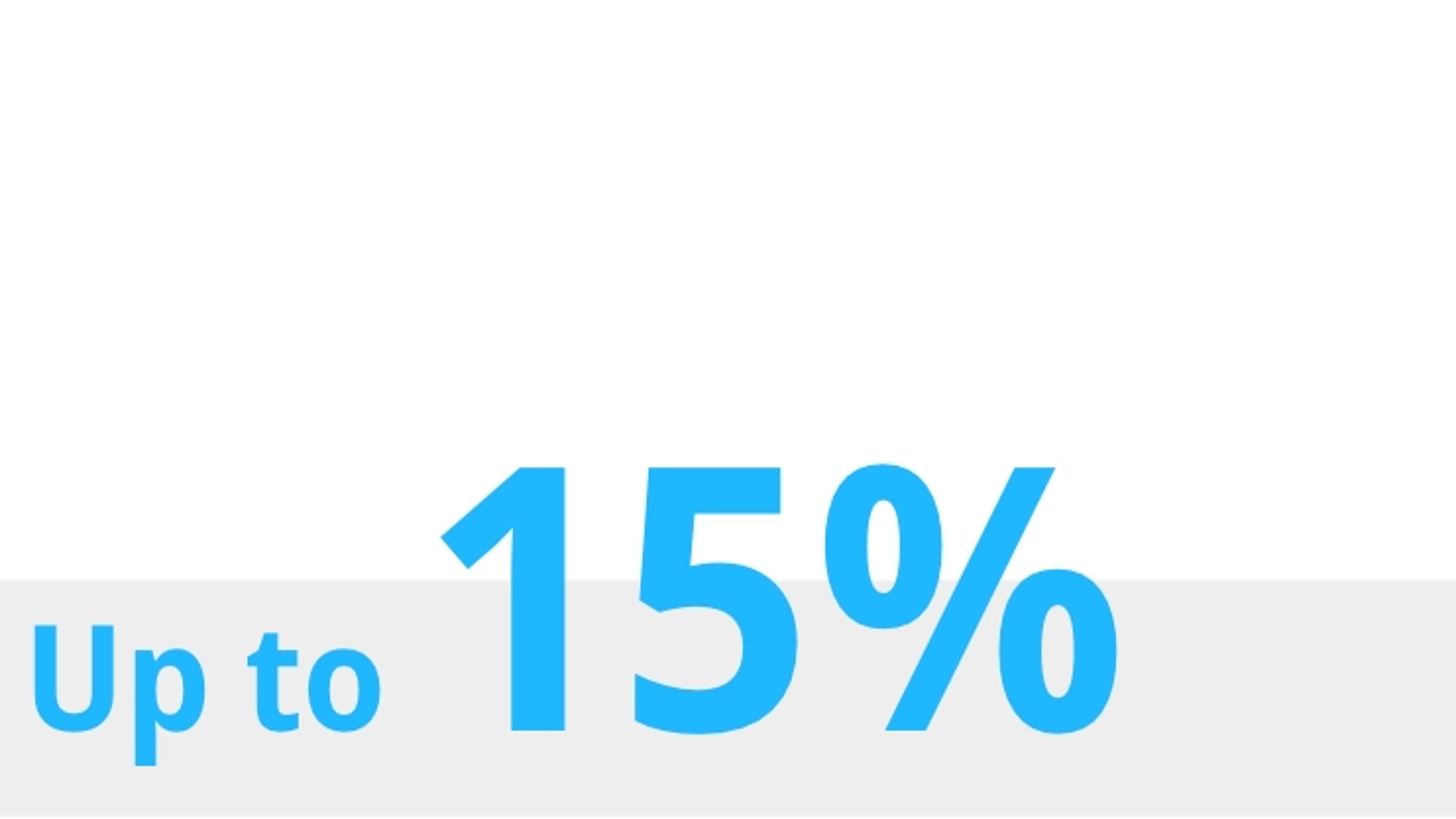
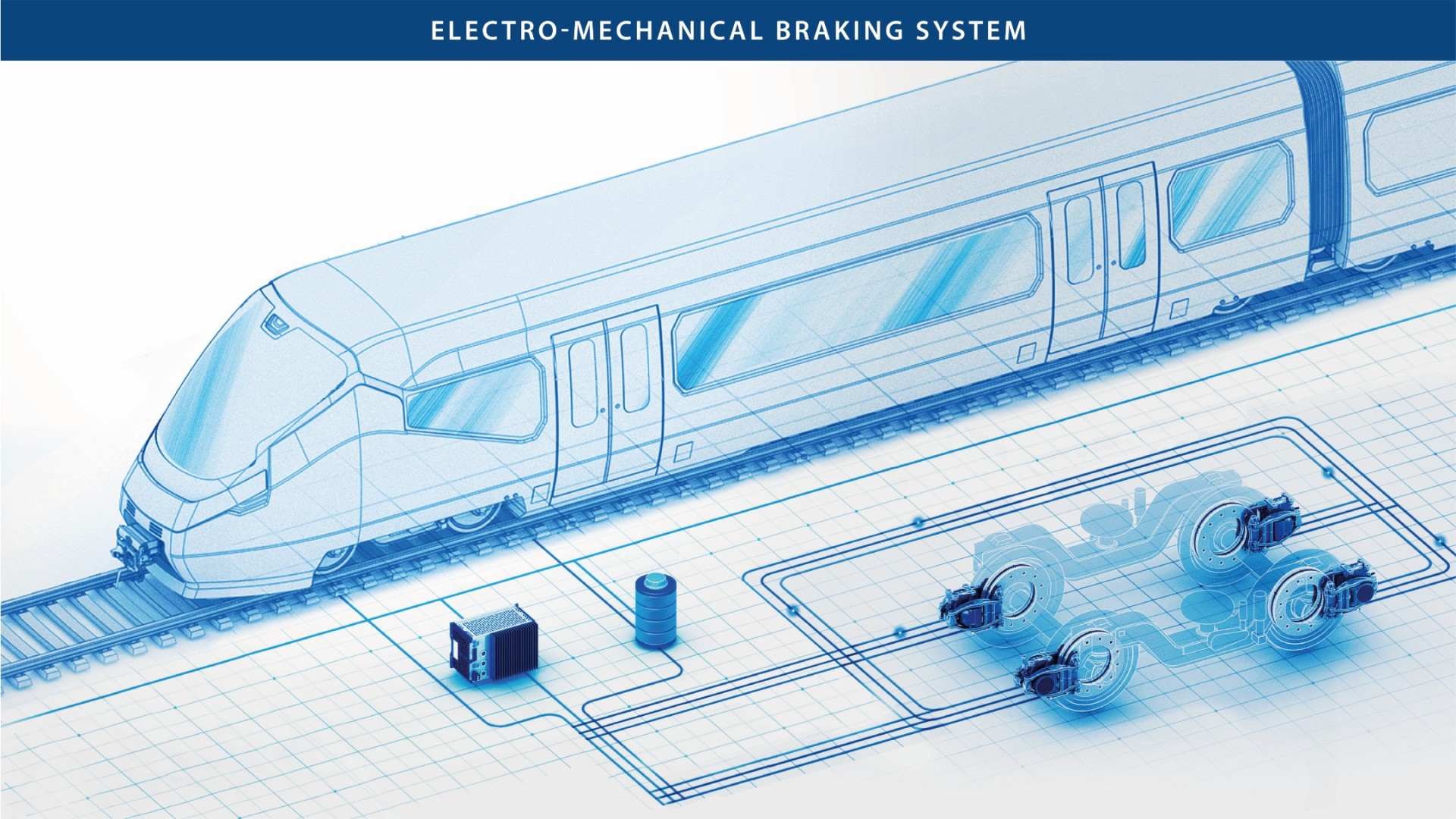
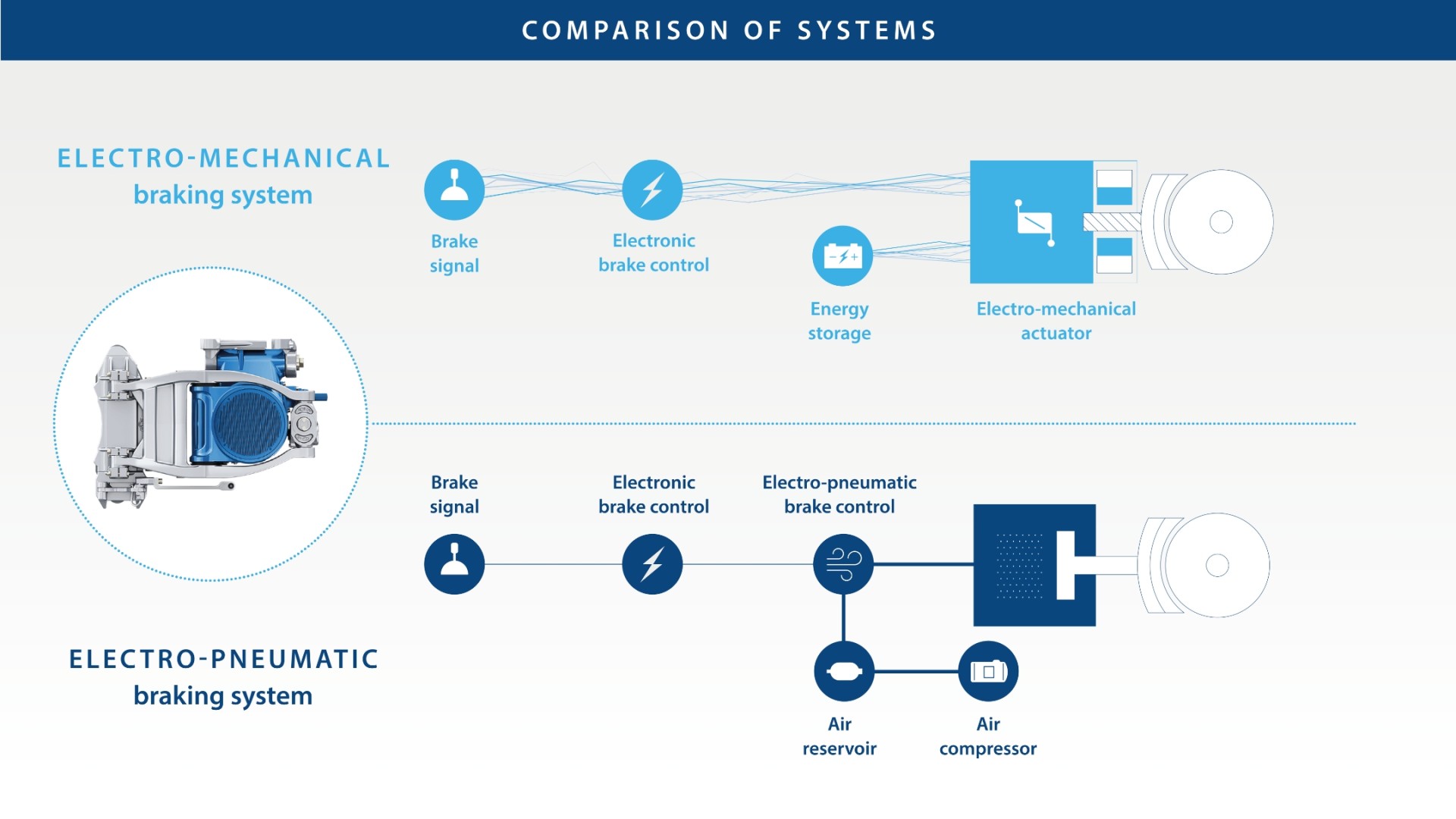
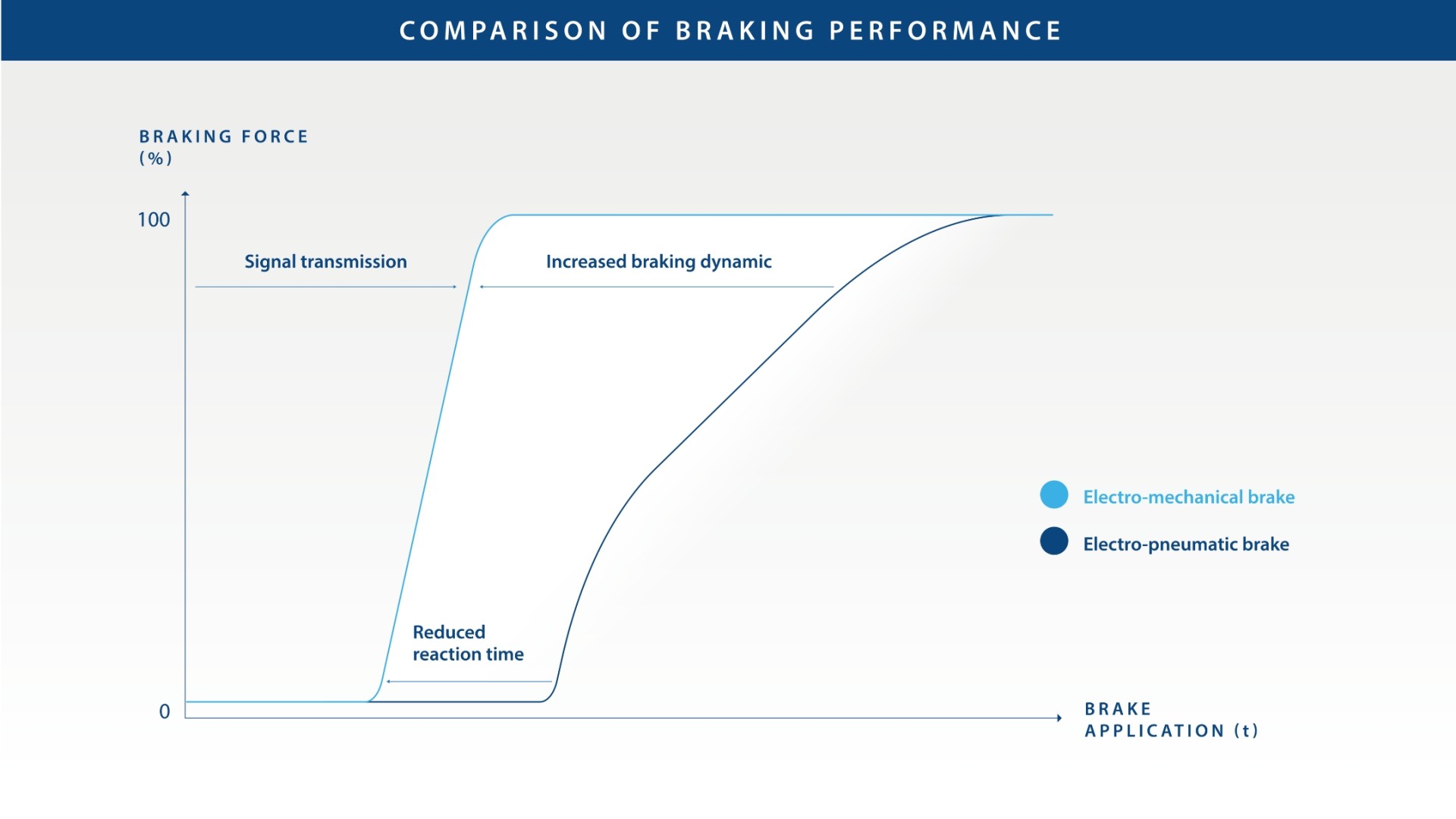
Does all this also have an impact on “total cost of ownership” – by which I mean the cost involved in purchasing a system and then operating it over a long period of time?
Matthäus Englbrecht: Yes. Quite simply because a system with significantly fewer individual components is less vulnerable, and also costs less to install in the vehicle and to maintain over decades of wear and tear.
And what about passengers? Will they feel any positive effects once EM brakes are installed?
Matthäus Englbrecht: Ideally, travelers won’t notice any difference. Because while we’re developing the EM braking system, we’re also pushing ahead with system innovations for electropneumatic brakes – such as Reproducible Braking Distance – that will interact intelligently with the rail infrastructure to increase train frequency, create more capacity, and make services even more punctual for passengers. The electromechanical brake is essentially a parallel evolution, representing another major braking technology with significant benefits and intended for a broad range of applications.
The EU innovation program Europe’s Rail Joint Undertaking, in which the 25 most important players in Europe’s rail industry are driving forward technologies for the rail services of the future, describes what it calls the “airless train” – meaning trains without pneumatic systems – as “healthier, safer and more attractive”. Why is that?
Josef Baier: Electropneumatic braking systems offer outstanding safety too, although electromechanical brakes are more than capable of matching it. Indeed, electropneumatic systems will still be in use decades from now. But for the reasons we mentioned earlier – lower weight, energy and space savings, connectivity enabling smart maintenance, greater potential for optimizing traffic flow – future train concepts are all calling out for new technologies. But even in the future, pneumatic systems won’t entirely disappear from trains.
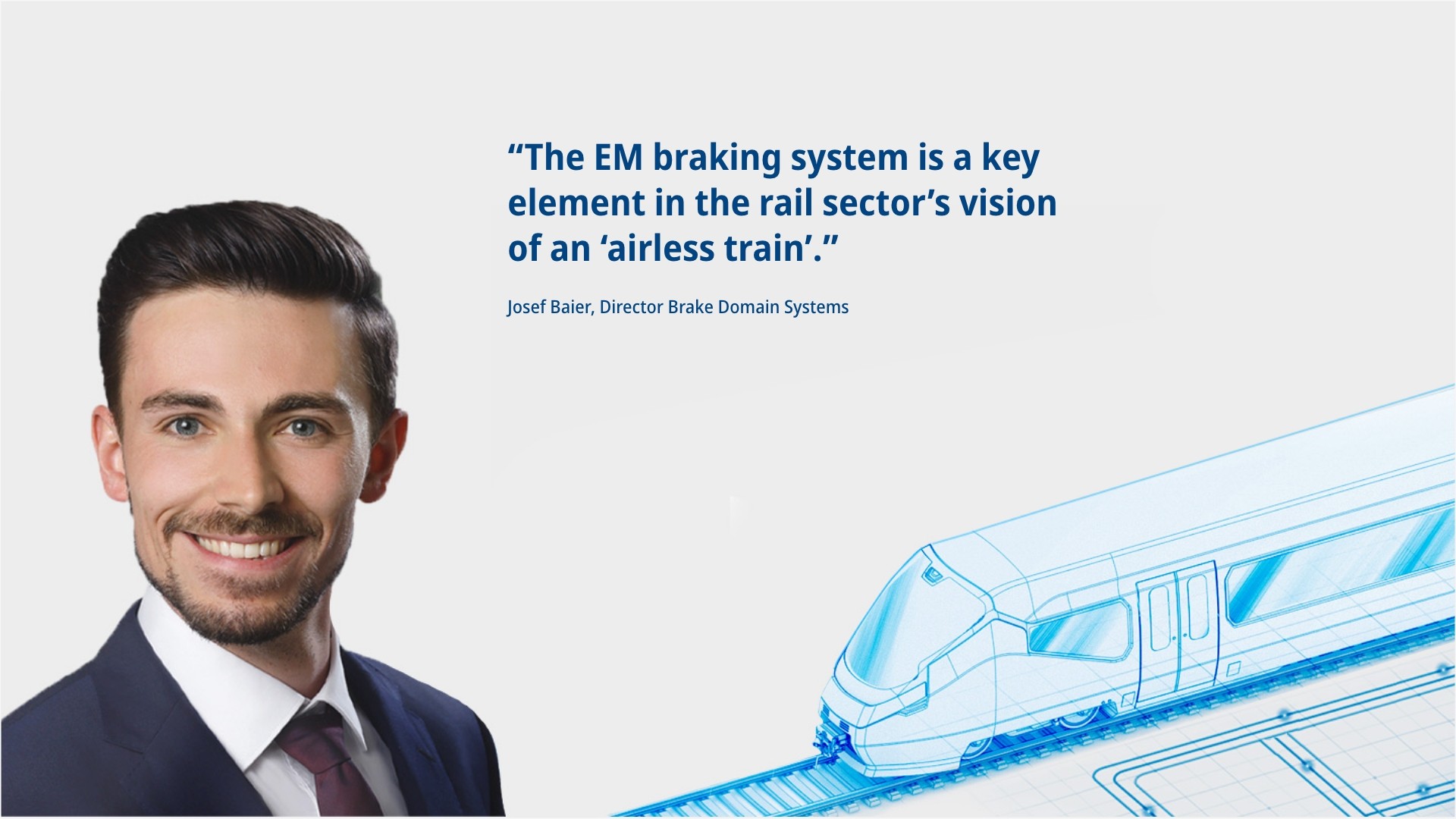
So there are other train systems that also need compressed air?
Josef Baier: Certainly – in train suspension, for example, or the pantograph control systems in light rail vehicles. Brakes are certainly the most complex pneumatic systems, but they’re not even the main compressed-air consumer. And even if the EM brake is a key element in the rail sector’s vision of an “airless train”, it’s perfectly possible that in the future small, highly efficient compressors could be used to generate compressed air locally for specialized applications. Examples include the vacuum technology in sanitary systems, which work the same way as in aircraft. In short, with the EM braking system, we’re taking an important step forward in paving the way for innovations that will benefit other compressed-air consumers, precisely because of the “airless train” scenario.
What steps are still needed to make the EM brake ready for real-world applications?
Josef Baier: The next major step is to put all of the EM braking system’s functions through rigorous tests on our large ATLAS test rig in Munich – the only one of its kind in the world. After that, probably in the first quarter of 2025, the system will be subjected to real-world, in-vehicle field trials over a period of several months. This will happen as part of the ERJU program we’ve already mentioned. We carried out preliminary test runs with the EM brake back in 2021, collecting valuable operating data in the process. Before we can bring the system to market, we also need to complete a number of complex approval procedures.
And what are the biggest challenges that still need to be overcome on the way to market readiness?
Matthäus Englbrecht: That’s obvious: to make the EM braking system as a whole so good that it can compete with well-established, highly optimized electropneumatic systems. And to do so cost-effectively while meeting at least the same standards of safety and reliability. We’ve got a very clear roadmap for achieving this.