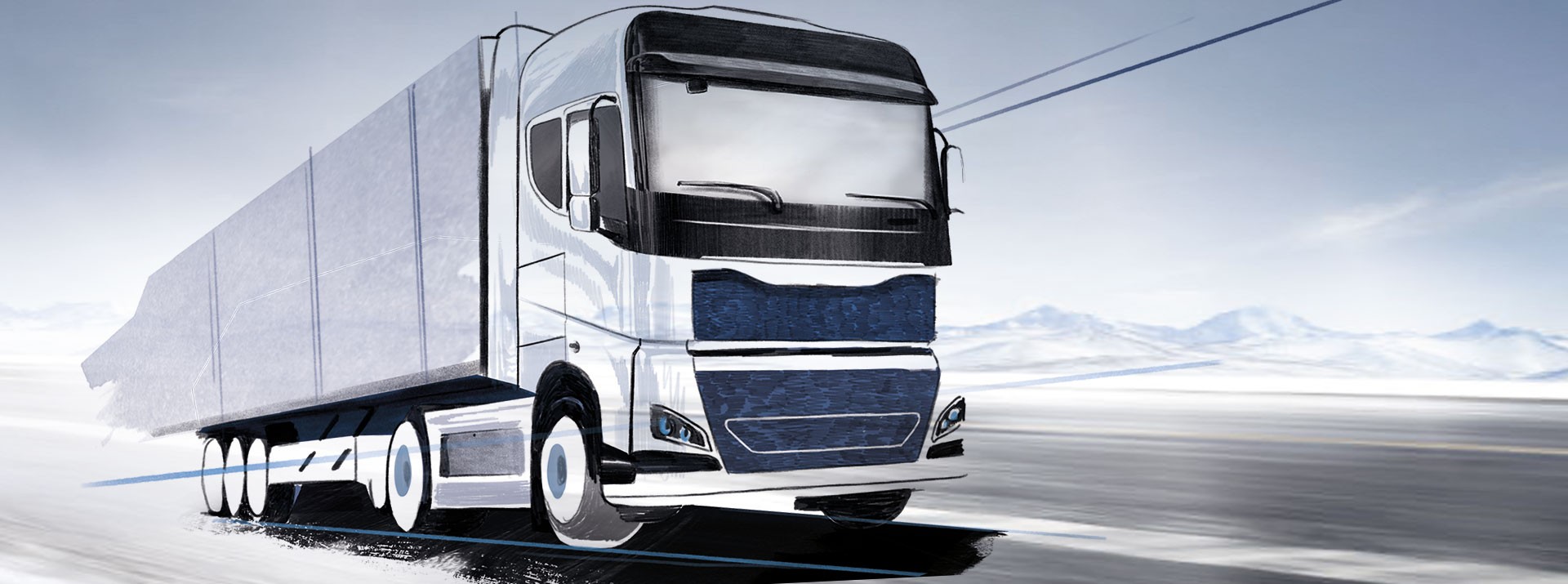
The new Global Scalable Brake Control system, or GSBC for short, clears the way for much simpler system layouts, fewer components and reduced weight. Above all, though, GSBC offers commercial vehicle manufacturers a future-ready platform to support upcoming driver assistance functions and highly automated driving.
For many years it has been standard practice for manufacturers to fit their vehicles with different braking systems in different countries. Even in the case of vehicles built for the global market, with the same basic modular design, in some countries a simpler Anti-lock Braking System (ABS) is the preferred specification, in others a more elaborate Electronic Braking System (EBS). This means working with two separate system architectures, and with separate version management for both products and software. Clearly, there has to be a more efficient way.
Harmonized system architectures
Global Scalable Brake Control (GSBC) marks a groundbreaking change of direction – from two systems to a streamlined, “one-size-fits-all” solution. This new brake control system reduces component proliferation by integrating all parts into a single technical platform. At the same time, however, GSBC’s modular component system still allows it to cater to the market demand for different versions. “The different modules can be combined and configured to match any required vehicle functionality and equipment level,” says Christian Urban, Vice President Center of Competence (CoC) Brake Control at Knorr-Bremse Commercial Vehicle Systems. “The harmonization extends all the way from mounting positions, electric wiring/pneumatic line routing and the positioning of connection points, right through to the individual components themselves.” As a result, the adaptation costs for manufacturers are significantly reduced, whether they are fitting a standard ABS system in a tractor unit or an ABS system with multiple additional functions in a multi-axle special-purpose vehicle.
More functions – up to 50 percent fewer parts
With its streamlining of components and modular overall system architecture, GSBC paves the way for more cost-effective system layouts. For a high-volume standard vehicle such as a two-axle semitrailer tractor, only half the previous number of components is required. “In addition to the savings on components and weight, further benefits for OEMs include significantly simplified installation in the vehicle and easier parts management,” explains Urban.
Knorr-Bremse has also streamlined the design of the central control unit, the nerve center of the system, where a further two functions – acceleration and yaw sensors – have been integrated directly into the control unit housing. For vehicle manufacturers, this further reduces the cost and effort involved in stocking and installing separate components.
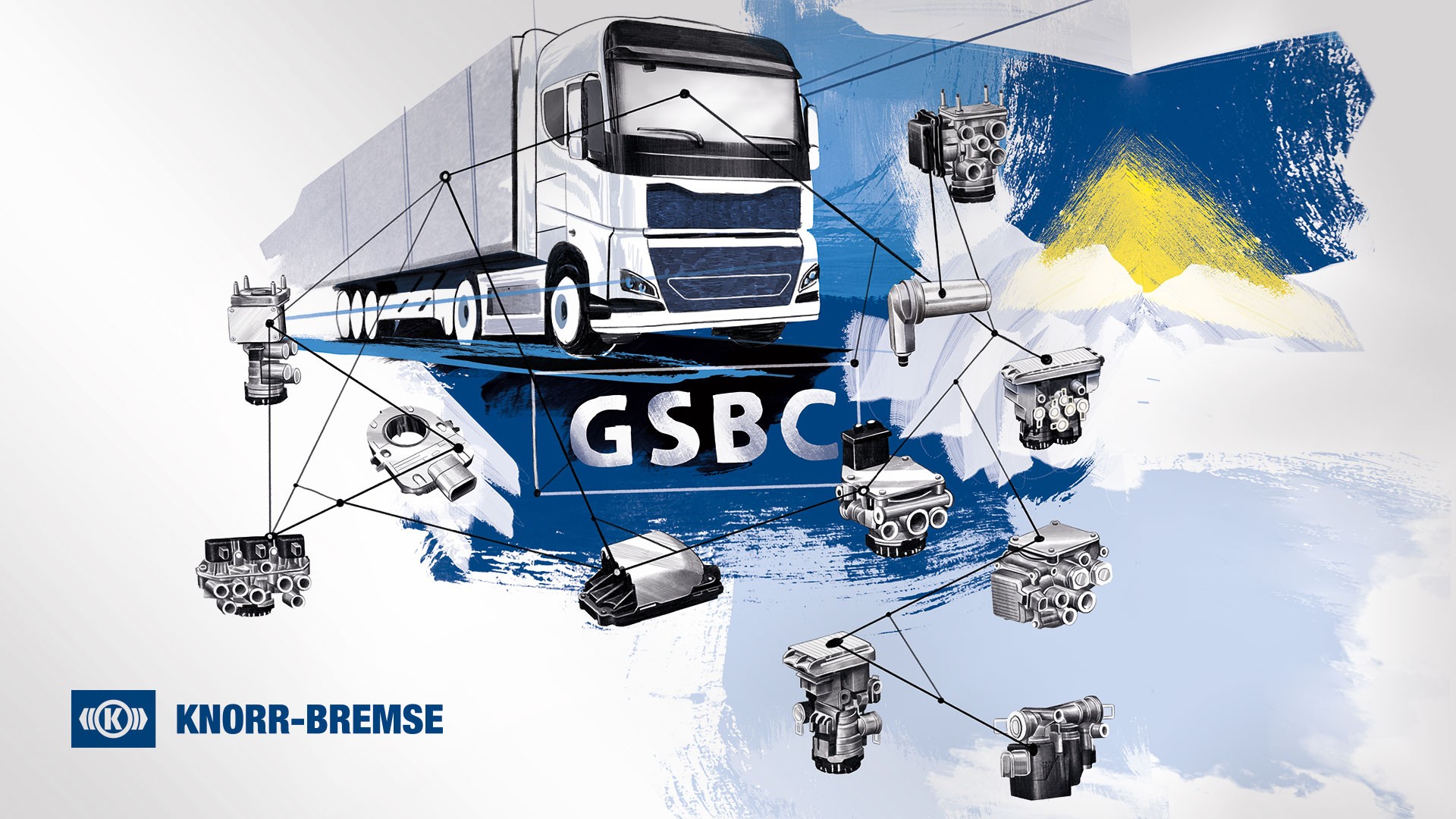
Self-learning system is future-ready for complex additional functions
While the passenger car market presents a relatively clear and transparent range of design variations, the diversity and complexity of versions in the commercial vehicle sector is huge. Many of the characteristics on which these versions are based, for example overall length, number of axles, wheelbase specifications, configuration as a solo vehicle or truck/trailer combination, center of gravity etc., must also be taken into account in the design of the braking system, and have a significant impact on vehicle dynamics and deceleration. If the braking system software were optimized for only one specific type of vehicle, it would have to be adapted manually for every individual vehicle version, creating a vast amount of work. Version management alone would consume a huge number of man-hours.
GSBC gets round all this by automatically adapting to different vehicle versions, using further-improved selflearning software functions and pre-defined parameter sets. “The new GSBC brake control system detects wheel spacing and steering geometry largely automatically. The software can then select the most appropriate parameters for the individual vehicle, thereby significantly reducing manual parameterization work,” says Jan Mayer, Head of Product Line ABS/EBS/GSBC at Knorr-Bremse Commercial Vehicle Systems.
Modular system for the software too
Just like the hardware components, the GSBC software, too, is based on a modular system. Here, along with systems already firmly established in the marketplace, such as ABS, traction control and oversteer/understeer compensation, the spectrum of functions also extends to features such as synchronization of the service brake and retarder (brake blending), hill start assistance, and automatic application of the brakes when a cab or bus door is open. Based on this modular infrastructure, implementing new functions is a very simple procedure. Customers can easily integrate entire function modules as an add-on to the GSBC hardware and software.
Platform for complex driver assistance systems
Driver assistance systems such as Adaptive Cruise Control, Emergency Brake Assist and Turn Assist are able to communicate with the GSBC system and the different braking functions. If, for example, Adaptive Cruise Control detects a significantly slower-moving vehicle in front, the system can use the GSBC software to apply the brakes.
An even more complex, and no less safety-critical application involves the integration of braking functions in the next generation of turn assist systems. Up until now, such systems have been confined mainly to issuing driver warnings, in the form of visual and audible alerts, and have not included automatic braking or steering intervention. However, the very limited space between the vehicle and road users moving alongside it means that in nearside-turning situations – which are the focus of such systems – the available reaction times for the driver are extremely short. But as Jan Mayer explains: “An integrated automatic system can take the necessary braking action even in situations where the time it takes for a driver to react means there would normally be no chance of doing so.” Such a function can prevent a collision by braking the vehicle automatically or, if necessary, using the integrated steering control to avoid a collision. For this application too, the modular software architecture of GSBC means that the relevant software module can be easily added and duly configured.
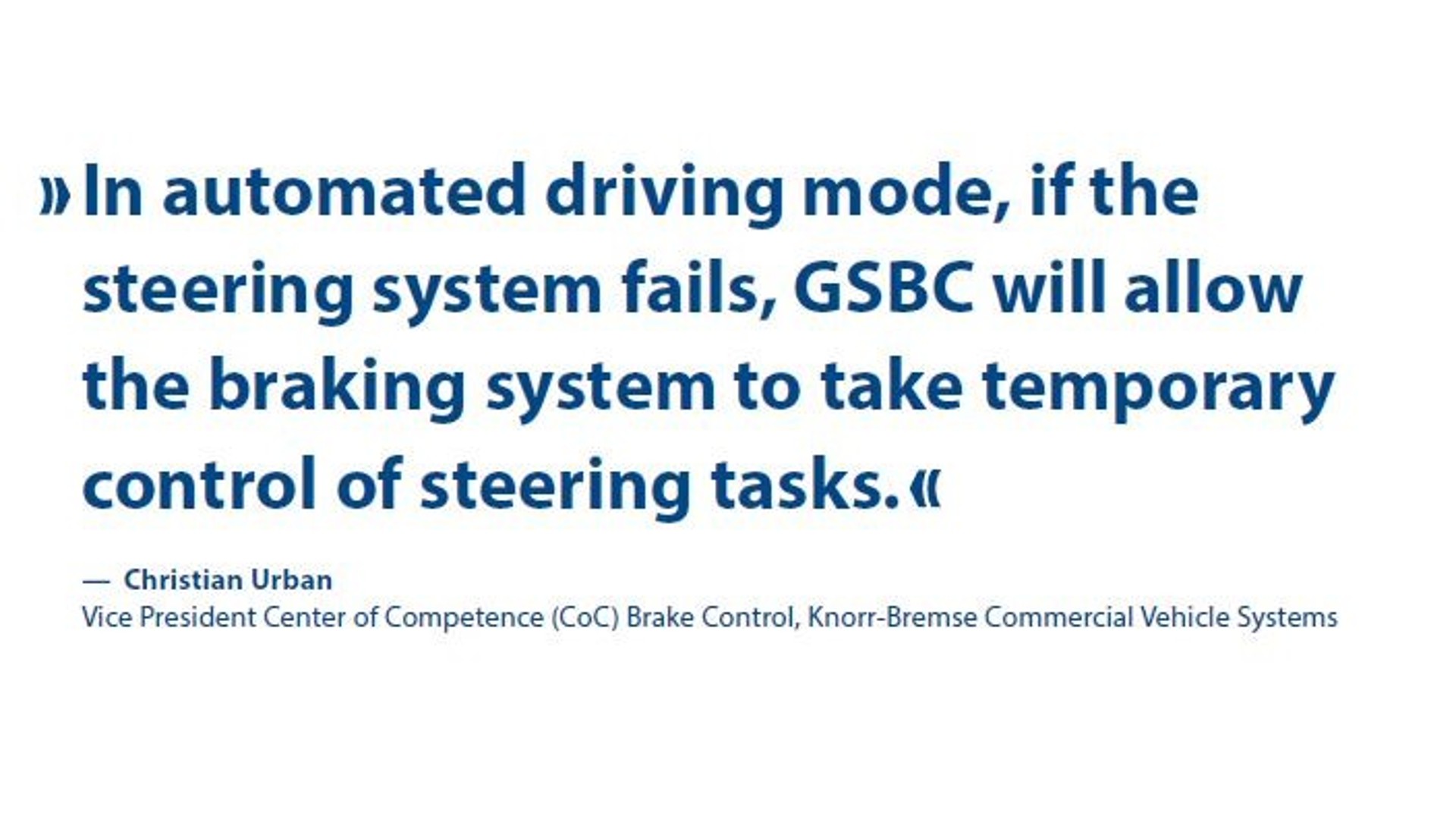
When the brakes act as a steering aid
The main function of a brake control system is to actuate individual wheel brakes. It performs this task by releasing a specific quantity of compressed air which closes the brake calipers on the selected wheels and squeezes the pads against the friction surfaces. “Not only can braking be used to decelerate the vehicle per se; it is also possible to use selective braking of individual wheels to produce a steering effect. For example, if a fully laden semitrailer rig is showing a tendency to understeer, continuing to head straight on rather than going round the corner, applying the brakes to the rear wheels of the tractor unit on the inside of the turn will correct the understeer,” notes Christian Urban.
Knorr-Bremse has refined this technique of brakebased steering to the point where a semitrailer tractor equipped with such technology was recently able to complete a full trip round a cornering circuit at the company’s Arjeplog test site in northern Sweden with no manual steering intervention. The associated software was integrated in the GSBC system. The system also included the Electronic Stability Program ESP, designed to prevent the vehicle from overturning, jackknifing or snaking. “For manufacturers, this kind of steer-by-brake system has great potential for the development of highly automated driving technology,” says Christian Urban. “The automatic system must be designed in such a way that whenever it takes over the steering, the vehicle cannot run out of control even if an electronic subsystem fails. And while installing a redundant steering system is not an economically viable proposition, the braking system is already on board. In future applications, our GSBC system, with its ability to handle steering tasks temporarily, will provide an extremely cost-effective redundancy solution.”
Braking and steering know-how under one roof
Knorr-Bremse is the global market leader for braking systems and continues to steadily expand its expertise in the field of commercial vehicle steering systems, as the following timeline shows:
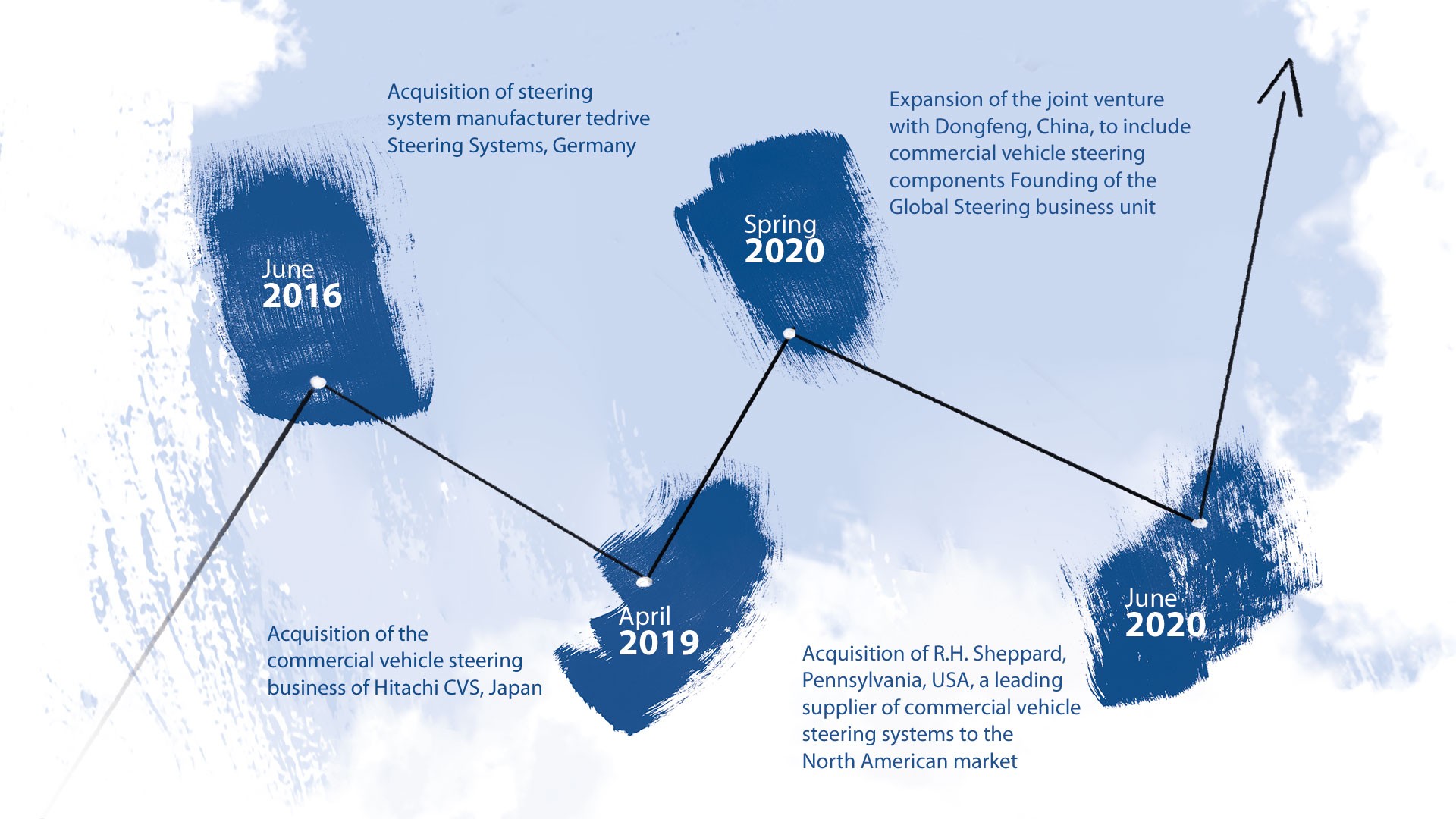
These acquisitions have strengthened Knorr-Bremse’s position as one of the world’s leading suppliers of commercial vehicle steering systems. Steering systems are also a key focus of work on the development of complex and highly integrated driver assistance systems (DAS) and highly automated driving technology (HAD).
Intelligent integration of brakes and steering
Since 2016, Knorr-Bremse has been steadily extending its systems expertise in the steering market, positioning itself as a one-stop provider of highly integrated systems and of new functions in the field of driver assistance and automated driving. In April 2019, Knorr-Bremse acquired the commercial vehicle steering business of Hitachi, Japan. This was followed in 2020 by the takeover of R.H. Sheppard, a leading supplier of commercial vehicle steering systems to the North American market. “For driver assistance functions and automated driving technologies, full control of vehicle dynamics is essential.
The most important actuator systems in this respect are the brakes and steering,” explains Urban. With the expertise of Hitachi and Sheppard, Knorr-Bremse has acquired a broad pool of global system know-how in the field of steering actuation, clearing the way for the development of complex driver assistance systems. And indeed, the first tests of the redundancy concept based on the new GSBC brake control system have already produced successful results.