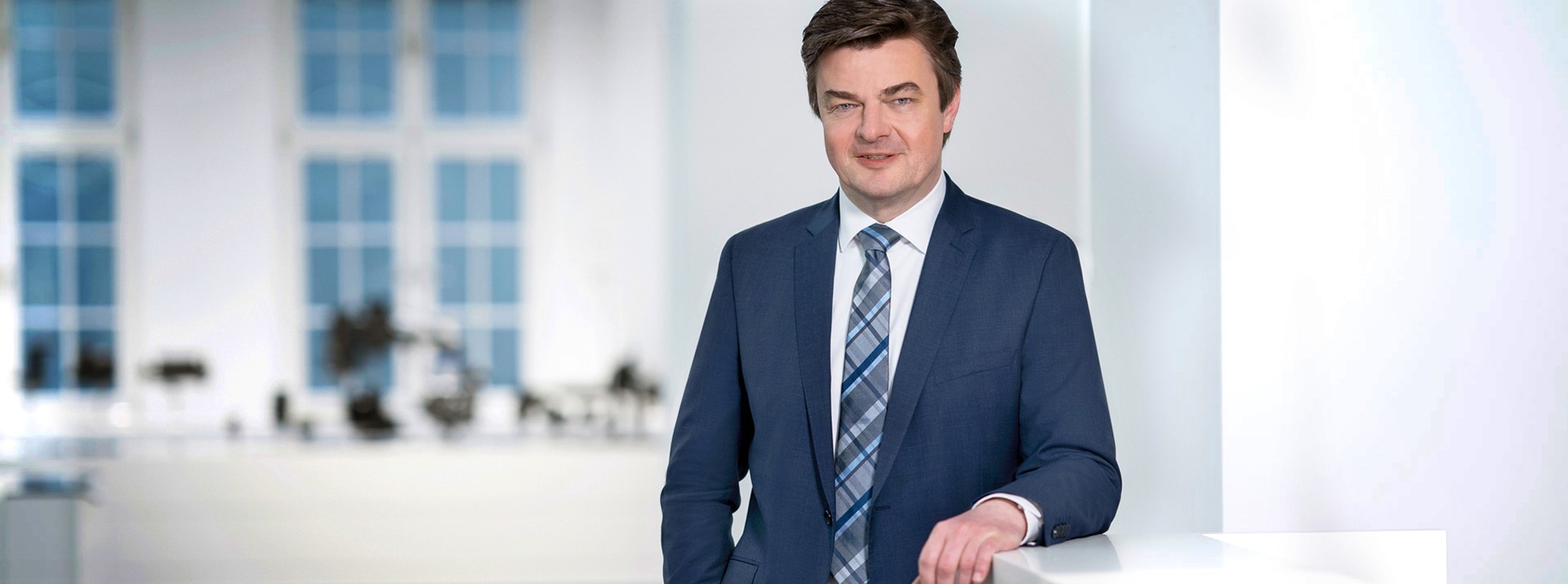
“The railways are a prerequisite for achieving climate-neutral mobility,” says Dr. Jürgen Wilder, Member of the Executive Board of Knorr-Bremse AG and responsible for the Rail Vehicle Systems division. | © Knorr-Bremse
Dr. Jürgen Wilder, member of the Executive Board of Knorr-Bremse AG responsible for Rail Vehicle Systems, is convinced that rail transportation is heading for further growth. Such growth, however, will mean increasing the capacity of the rail network. Innovations in braking systems and other vehicle components will help to create that extra capacity.
Info
The original interview was published in the magazine "EISENBAHNTECHNISCHE RUNDSCHAU" (ETR) No. 12/2020.
Knorr-Bremse’s Q3 balance sheet shows an EBIT margin of 18.4% for the first nine months. How did that come about?
We were quick to introduce cost-cutting measures, not least in terms of fixed costs. And of course that’s reflected in our EBIT. Another positive impact came from the sale of the Powertech company that still appeared on the first-half balance sheet in 2019. But by far the most influential factor was that, ever since the onset of the coronavirus crisis – a pandemic the likes of which we have never seen before – the rail sector has been classified worldwide as infrastructure of systemic importance. Trains continue to run reliably, keeping the lifelines open across the various countries, even if at certain times of day they are virtually empty. Even empty trains need brakes! Particularly in the early days of the crisis, rail operating companies were worried that their supply chain wouldn’t prove stable enough and so they stocked up on spare parts. This strengthened the performance of our Service business unit, particularly in Q2 2020. With the warehouses now better stocked, we could see a slight slowdown here in the final quarter. Of course we’ve witnessed an overall drop in revenues, but compared to other industries we have come through recent months and the first lockdown period well and profitably. The rail sector has proved crisis-proof.
Is Knorr-Bremse working on developments that could help to make trains more resistant to the pandemic?
Yes, of course. Airflow, filtration and purification systems are of central importance here. Viruses adhere to carrier mediums which can be filtered out effectively by climate control systems. And then there is ultraviolet light which can be used to kill off viruses. Filters and UV lighting can be retrofitted to existing trains, while in new vehicles we can also control the airflow in such a way that viruses are not distributed around the entire car and instead filtered out rapidly. That said, so far there haven’t been any spreader events on trains. Studies show that traveling by train is safer than flying, particularly with the latest technology on board.
The rail sector is of systemic importance. Given the immense financial outlay that governments across the globe are having to make in order to offset the economic impact of the coronavirus pandemic, isn’t there still a risk that governments, in India for example, will postpone planned investments in rail vehicles owing to a lack of funds?
There have indeed already been budget cutbacks in India, but at the same time orders for spare parts increased in the first half year, with a view to sustaining vehicle maintenance. Looking to the medium and long term, I’m optimistic that we will not be seeing any large-scale downturns in demand. Once the coronavirus crisis is overcome, demand for climate-friendly mobility will be back on center stage and the debate on reducing carbon emissions will reopen. The focus will once again be on shifting traffic from road or air onto the rails. The railways are a prerequisite for achieving climate-neutral mobility. The big question for our sector will be how to create the capacity required for this modal shift. Sources of funds will basically be available − in Europe through the Green Deal or in Germany through the “rail pact” concluded between government and the rail industry.
Where could problems arise?
Firstly, it’s good that we’re setting ourselves such ambitious goals as doubling rail passenger transportation by 2030 and shifting the modal split in the freight sector from a current 18% to 25% by rail. If we then also take account of the overall growth in the volume of freight traffic, this will mean almost doubling rail freight transportation by 2030 as well. It must be said, though, that compared to road, the framework conditions for rail are much more demanding. Quite apart from track access charges, there are interoperability issues at the border and train drivers need at least a basic knowledge of the local language – not something you encounter on the road.
Isn’t ETCS going to help to resolve the technical compatibility issues at the border?
Efforts to create ETCS corridors with harmonized technology have been going on for years. It’s a long, slow process and costs a great deal of money. Of course ETCS means that traffic density can be increased. But ETCS is not the only technology that can boost rail network capacity – there are also vehicle-borne innovations that can be implemented faster.
Which innovations is Knorr-Bremse working on that will help to increase network capacity?
In the next few years, we’re aiming to launch our Reproducible Braking Distance Management System that will guarantee that a predefined braking distance is maintained, whatever the weather. We’re working at the track/wheel interface here – much like ABS systems in road vehicles do; so the brakes work with pinpoint accuracy, leading to shorter braking distances.
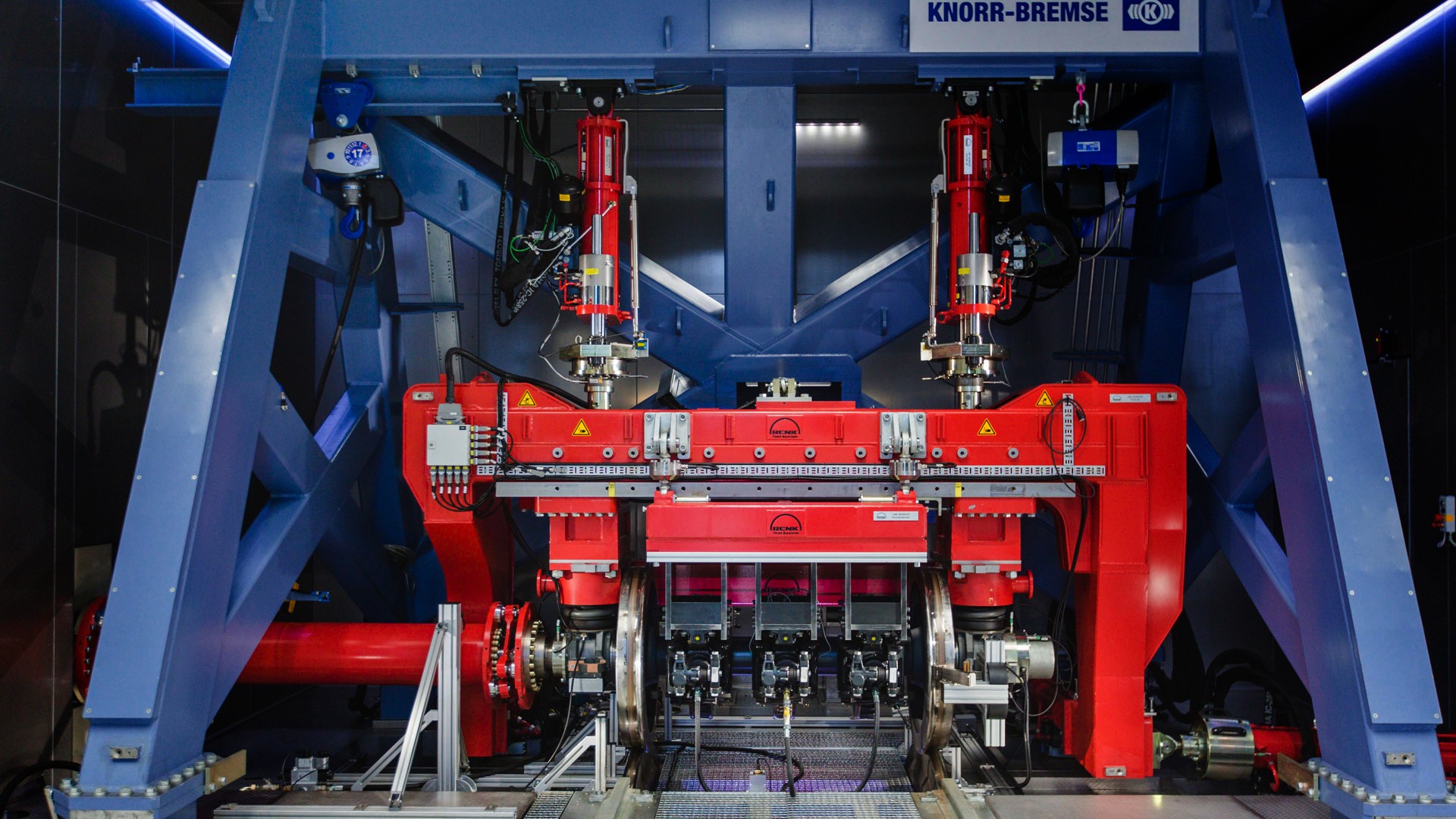
That means the safety distance between trains could be reduced…
Exactly. With current braking technology, in each case the longest of the various possible braking distances must be taken as the safety distance when the blocks sections are defined. So if a commuter train in Munich has a braking distance of 600 meters in dry weather, its braking distance in the wet, with leaves on the track, can be as long as 2,000 meters. And these 2,000 meters determine the headway. If, through smart connectivity, our Reproducible Braking Distance Management System can guarantee a braking distance of 800 meters, then theoretically up to twice as many commuter trains could operate on the network, without having to invest in new infrastructure.
You’re saying that changes in braking technology alone could double the network capacity?
Doubling the capacity will not generally prove feasible in practice. But where there are bottlenecks in the network, much like with ETCS, new braking technology can lead to a 20-25% increase in capacity. Combining the two technologies would lead to a substantial increase in network capacity, and that is always going to be less expensive than investing in the construction of new sections of track, to say nothing of the long-drawn-out approval procedures and public protests over expansion of the rail infrastructure. Apart from which, installing new brakes in the vehicles would not only boost network capacity but at the same time help to reduce noise emissions from the railways, thereby leading to wider acceptance of rail sector growth among the general public.
Major procurement orders for rail vehicles have already been awarded. Are these vehicles already going to be fitted with the new braking technology?
We’re not quite there yet, but our research findings to date are very promising indeed. We’re aiming to bring the new braking technology to market in the course of the next few years.
Will the brakes that are to be installed in the vehicles currently on order be able to meet these requirements?
Not at the moment. But that will soon change. We’re think very long-term in this respect.
What can be done in the shorter-term?
Another way to increase network capacity is by improving the reliability of components such as the doors. Fewer problems with the doors mean fewer delays, scheduling becomes more stable and any reserves built into the timetable to accommodate such issues are freed up. There are various technical solutions here that we take into account in our development and production activities. One such measure is redundancy – the duplication of critical components. Another is to design the components in such a way that they can be rapidly replaced, without the whole train having to return to the depot. Then there is preventive servicing and maintenance, courtesy of digitalization, and mobile service teams – all designed to increase the reliability of the components we supply.
Component reliability is a topic close to the hearts of the vehicle manufacturers too, who increasingly offer guaranteed availability.
That is indeed a strong trend. Added to which, when contracts are awarded, the decision is often based not least on life cycle costs, that is to say the costs incurred for servicing, for example, over the entire service life of a train or component. So if, through our life cycle management measures, we at Knorr-Bremse can help to cut the life cycle costs of braking systems, doors or HVAC systems, then in turn the vehicle manufacturers can submit attractive offers to those operators who increasingly focus on such criteria in their invitations to tender.
As the coronavirus crisis has shown, a situation with fewer malfunctions and thus fewer delays in the passenger sector has also benefited freight transportation which has also been more punctual, as more trains ran on schedule.
Exactly. When passenger trains are generally more able to run on time, that leads to an improvement in punctuality for freight trains as well. Although it must be said that in many areas rail freight traffic is not run profitably, nor can it be. Further major investments in improving efficiency are called for here – investments in digital automatic coupling (DAC), for example.
What is Knorr-Bremse’s interest in DAC?
Last year we announced our intention to enter the coupling business, and we’ve already executed several research and development projects for the passenger sector. And with the topic of digital automatic coupling now being widely assigned greater importance, we have decided that Knorr-Bremse too will develop a DAC.
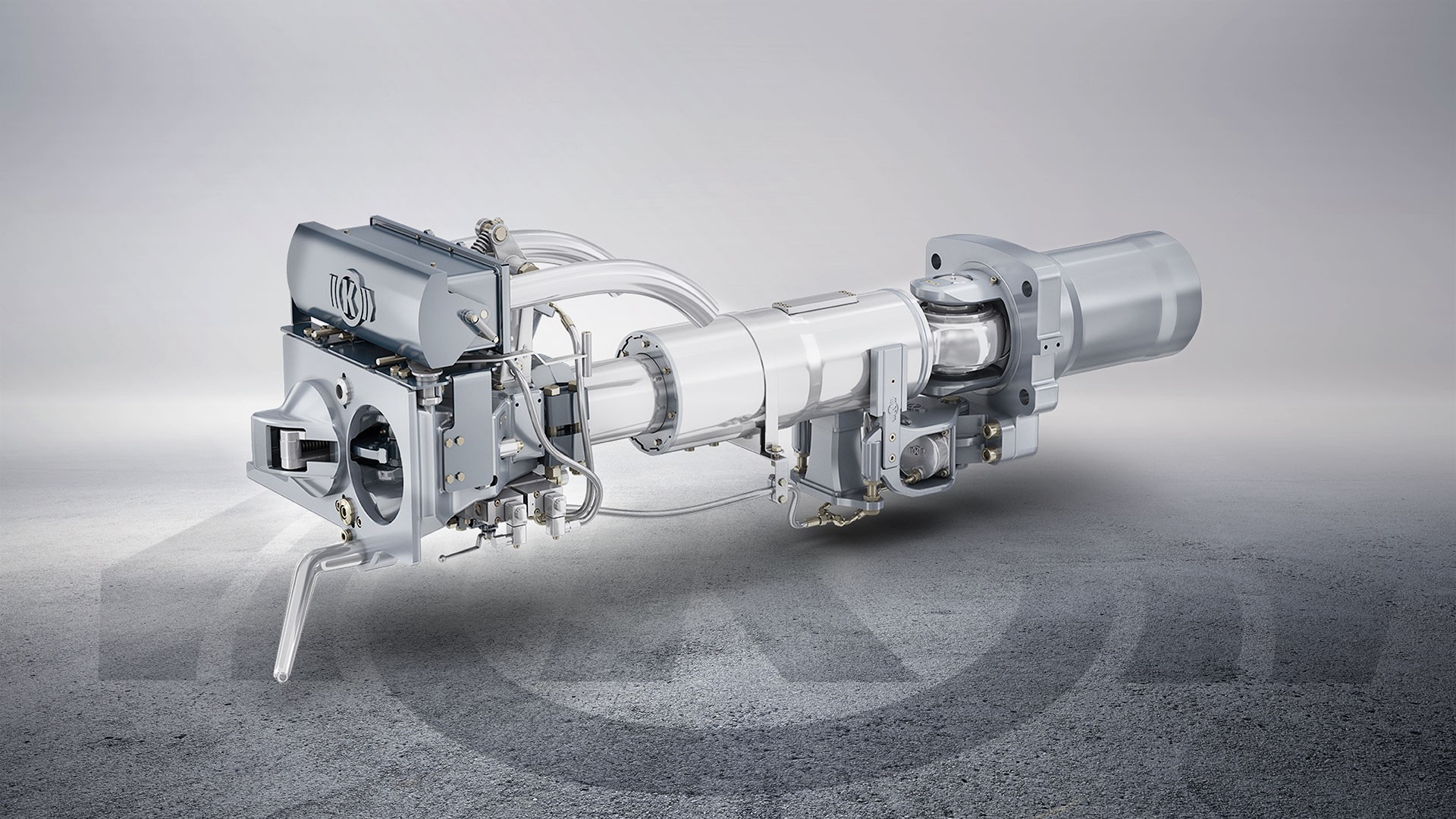
Three types of coupling are currently being trialed, before early in 2021 a decision is made in favor of one of them. So what makes you think there is still room for a DAC from Knorr-Bremse?
We’re involved in all the discussions concerning DAC and are following developments very closely. Even when the decision is taken in favor of one type of coupling, that doesn’t mean to say that only one manufacturer will produce them. When you consider that certification procedures and migration to the new technology will also take several years, we are convinced there is still sufficient time for us to become a significant DAC supplier.
Will the introduction of 5G or FRMCS change anything for Knorr-Bremse and its components?
Definitely. We need more and more smart products. That’s why we have invested in companies such as Rail Vision and Railnova. Railnova’s fleet management software is currently installed in 1,500 locomotives in Europe. From the data acquired there we can glean new knowledge relating to preventive maintenance. Rail Vision develops real-time image processing based on artificial intelligence. So with the help of sensor systems from Rail Vision, network operators can tell, for example, where greenery needs cutting back to avoid operations being disrupted by storm damage. And to be able to develop this kind of business model in the future, we are going to need very fast data transmission.
Climate care is sure to remain a long-term trend. What does that mean for Knorr-Bremse?
We don’t just want to contribute to climate care through our products. By focusing on energy efficiency, generating our own energy from renewables and buying in energy – also sourced from renewables –we are also aiming to halve emissions of carbon dioxide for the company as a whole by 2030. On top of this, not least through carbon offsetting, we plan to become carbon neutral by 2021. And we’re going to be assigning greater priority to the topic of sustainability in general.
What proportion of Knorr-Bremse’s logistics is handed by rail freight and how much potential is there to increase that?
In our Rail division we make use of rail freight transportation where possible and most recently in 2020 we were able to expand our use of rail freight between Europe and China. This was primarily because we shifted shipments on this route that would normally go by sea onto the rails in order to safeguard our supply chains during the coronavirus crisis. But of course on account of the last mile we still have a fair proportion of truck transportation. Which is another indication that the rail freight sector needs to address the issue of the last mile.
Looking at Knorr-Bremse as a whole, revenues for the Truck and Rail divisions are at approximately the same level. Is that the way you intend things to stay, going forward, or will the growth of the rail market also be reflected in a larger share of revenues?
This year, we are, of course, witnessing a shift in favor of rail, because the commercial vehicle sector is much harder hit by the coronavirus pandemic that the rail vehicle sector. That said, we believe that we will see an overall increase in the volume of freight for transportation, from which both divisions of Knorr-Bremse stand to profit in the future. Traditionally, we have a revenue split of 53/47% in favor of rail. This year the split will more likely be in the region of 60/40%.
And finally a personal question: What has changed for you personally as a result of the coronavirus pandemic?
I’ve learned to break with old habits: I travel less, of course, and my interaction with colleagues and customers has become more virtual. With a few exceptions, this works very well and it also saves time and resources. In the post-coronavirus period, these experiences will help us to work more efficiently and use fewer resources − and not slip back into those old habits.
Info
Dr. Jürgen Wilder, Member of the Executive Board of Knorr-Bremse AG
Since September 2018, as a member of the Executive Board of Knorr-Bremse AG, Jürgen Wilder has held global responsibility for the Rail Vehicle Systems division. Previously, from 2015 to 2017, Wilder, who holds a doctorate in Physics, was CEO and Chairman of the Managing Board of DB Cargo and as such responsible for Deutsche Bahn’s worldwide rail freight operations. After obtaining his Ph.D., he worked as a research fellow at Harvard. His first role in the business sector was with Siemens. Here, he held positions including CEO Rolling Stock Business USA, Head of Strategy Infrastructure and Cities Sector, and, prior to joining DB Cargo, CEO Global Business Unit Mainline Transportation.