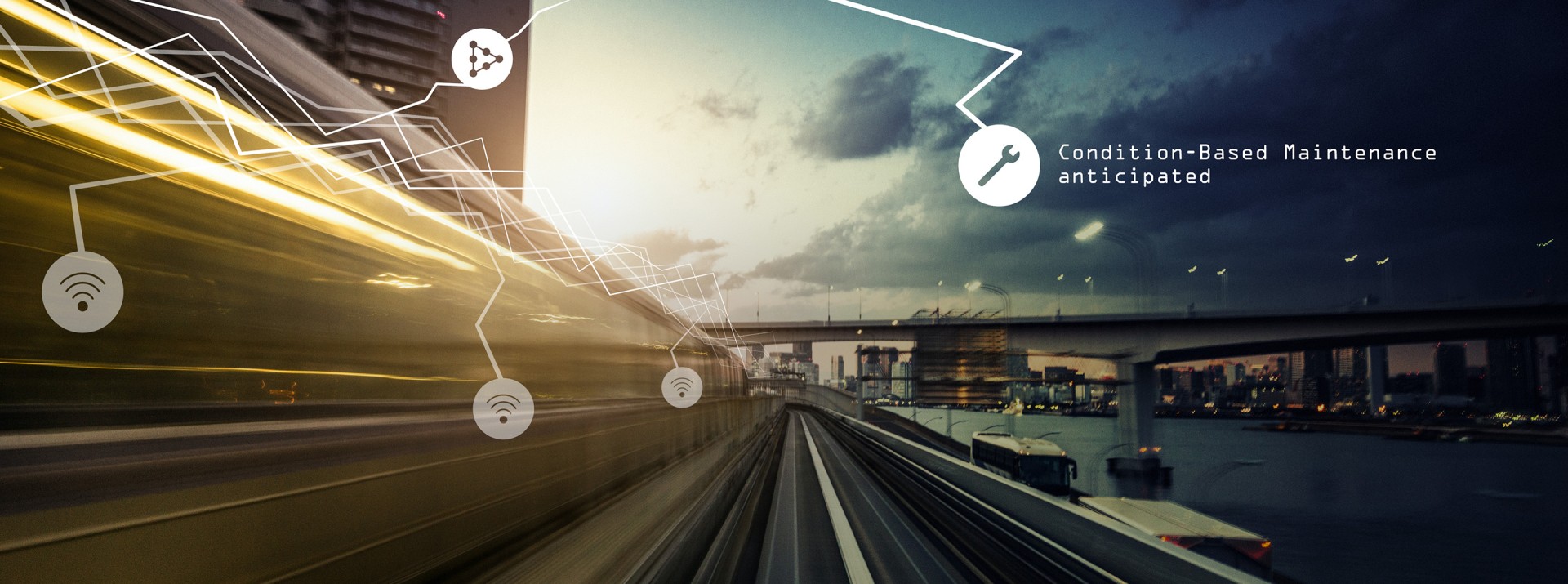
Digitalization is opening up all kinds of intelligent, practical solutions to many of the challenges facing the rail industry. Knorr-Bremse is focusing on approaches involving data-driven systems – developments that are already adding plenty of value today. And have enormous potential for the future.
The exponential increase in computing power and storage performance in recent years has made it possible to use data in very different ways from before, across all walks of life. The results are astounding. The future is becoming predictable, fulfilling one of humanity’s oldest dreams. Admittedly on a small scale – but one that is directly relevant to the rail industry. To take just one example: Train maintenance – hence also the availability of trains on the network – can be hugely improved thanks to precise predictions generated by smart data analytics. As mobility continues to evolve, this is a major milestone. Knorr-Bremse is systematically investing in such data-driven products and smart processes. The resulting benefits for customers, and for the Group itself, are huge.
Data-driven added value – for customers and Company alike
Developed by Knorr-Bremse’s Rail Vehicle Systems division, this data-driven innovation is known as Condition-Based Maintenance (CBM), describing a form of maintenance based on a rail vehicle’s current and predicted status. “With respect to the dataset required for this kind of solution, Knorr-Bremse – as a leading supplier of brakes, entrance systems, HVAC systems, sanitary facilities and control-system components – has a priceless advantage: We’re sitting right at the source,” explains Dr. Maximilian Eichhorn, Vice President Digital Products at Knorr-Bremse. “This is where you find true value in the digital age – in the subsystems installed on trains.” These subsystems generate large quantities of operating data while the trains are running. “This data allows us to measure and manage the condition of our systems and predict their behavior – all in real time, while the train is in operation.” The invention is nothing less than a turning point for Knorr-Bremse, its customers, and the train industry as a whole.
Condition-based maintenance – and the next step into the future
Just how CBM works is explained by Markus Schumann, Director Sales Digital Products & Services at Knorr-Bremse: “Sensors can accurately capture data generated by, for example, vibrations, oscillations, energy consumption, noise, temperature variations and many other sources. The captured data is bundled and transferred to the Knorr-Bremse Cloud platform, where it’s analyzed by self-learning algorithms – essentially a very precise artificial intelligence system – and made available to our customers as insights. That’s how we inform them of the ‘healthiness’ and performance of the various systems.” CBM enables rail operators to maintain their train fleets more efficiently. Potential defects can be identified and proactively rectified at an early stage, rather than when they are just about to cause a malfunction. In short, this is maintenance based on real-time status. “And we can go a step further,” adds Stefan Soyka, Director Digital Development & Services, “because in certain cases, our algorithms already allow us to very accurately predict when components will need to be replaced in the future.”
Manufacturers and operators all benefit. CBM enables them to reduce costly downtime and depot time, optimize rail vehicle operating and lifecycle costs and – thanks to precise tracking of system performance – save energy. Rail operators can offer their passengers higher availability, with more trains on the line at any given moment. This is how Knorr-Bremse adds value for customers. And there is more: “New kinds of digital business models are one of the core drivers of our own business,” says Maximilian Eichhorn, “because our customers are prepared to pay for the enormous benefits provided by these products and services.”
UK rollout of remote condition monitoring for HVAC systems
Including customers in the UK, for example. Here, the rollout of a Remote Condition Monitoring (RCM) solution – a precursor of CBM – is in full swing. A total of 733 HVAC systems supplied by Knorr-Bremse’s Merak brand are being modernized and upgraded in 172 trains built by Siemens Mobility for English rail operator South Western Railway. The upgraded systems use sensors to capture data on ambient temperature, temperature inside the train, system performance, energy consumption, and the CO2 content of the air in train compartments. “The Knorr-Bremse Cloud analyzes this data algorithmically and transfers the results via an interface to Siemens Mobility’s Railigent rail asset management platform, where they’re displayed on dashboards,” explains Markus Schumann. “This allows Siemens Mobility – who in this case are also responsible for maintaining the systems – to assess their condition and make maintenance-related decisions.” In addition to other indicators, the Knorr-Bremse Cloud uses a traffic-light system to highlight the condition of the monitored components. They are assigned red, yellow or green status, depending on how soon they need to be serviced. Knorr-Bremse devised the concepts behind this monitoring system in close consultation with train operators – it also covers entrance systems, braking system components, air compressors and brake blocks.
Digital ecosystems offer unlimited opportunities
These steps toward a digital ecosystem – comprising a network of different partners offering various digital services via an intermediary platform – are laying the foundations for many other digital solutions. South Western Railway, for instance, is planning to save more energy by using sensor-gathered data. “We can already tell how many people there are in a railcar from the CO2 content alone,” explains Maximilian Eichhorn. “If there are only a few, we can turn down the system settings. This represents a significant energy and cost saving for operators – after all, HVAC systems are the second biggest energy consumer in a train after the traction system.” From RCM to full condition-based maintenance is only a short step. And Knorr-Bremse could encourage customers to upgrade by offering a performance guarantee promising, for example, near-100% availability. The technology is already under intensive development, and solutions can always be adapted to customers’ highly specific needs.
For example, Knorr-Bremse already offers a Predictive Maintenance service – a higher level of digital maintenance – for train entrance systems supplied by Knorr-Bremse’s IFE brand. In this case, the smart Knorr-Bremse Cloud makes even more precise predictions about when a given component is likely to fail, and with what degree of likelihood. In the case of train doors, for example, it clearly specifies how many opening and closing cycles remain before the doors will need maintenance, making it even easier to schedule service intervals. Stefan Soyka is anticipating further developments: “In the future, the systems Knorr-Bremse is currently working on will be capable of analyzing the data they’re generating on their own, and then sending their ‘smart’ maintenance predictions and recommendations to the higher-order platform.”
“Intelligent systems and components are the future,” adds Maximilian Eichhorn. “You can imagine them as being a bit like smartphones. The functions we expect to offer with them will depend on which applications – or apps, as it were – we install on them, how we use the data they generate, and what other scalable solutions we can develop for our customers based on these apps and data.” Which just goes to show: There are no limits to the possibilities and opportunities. The digitalization of the rail industry is going full steam ahead. And this is just the beginning.
CONTACT PERSONS:
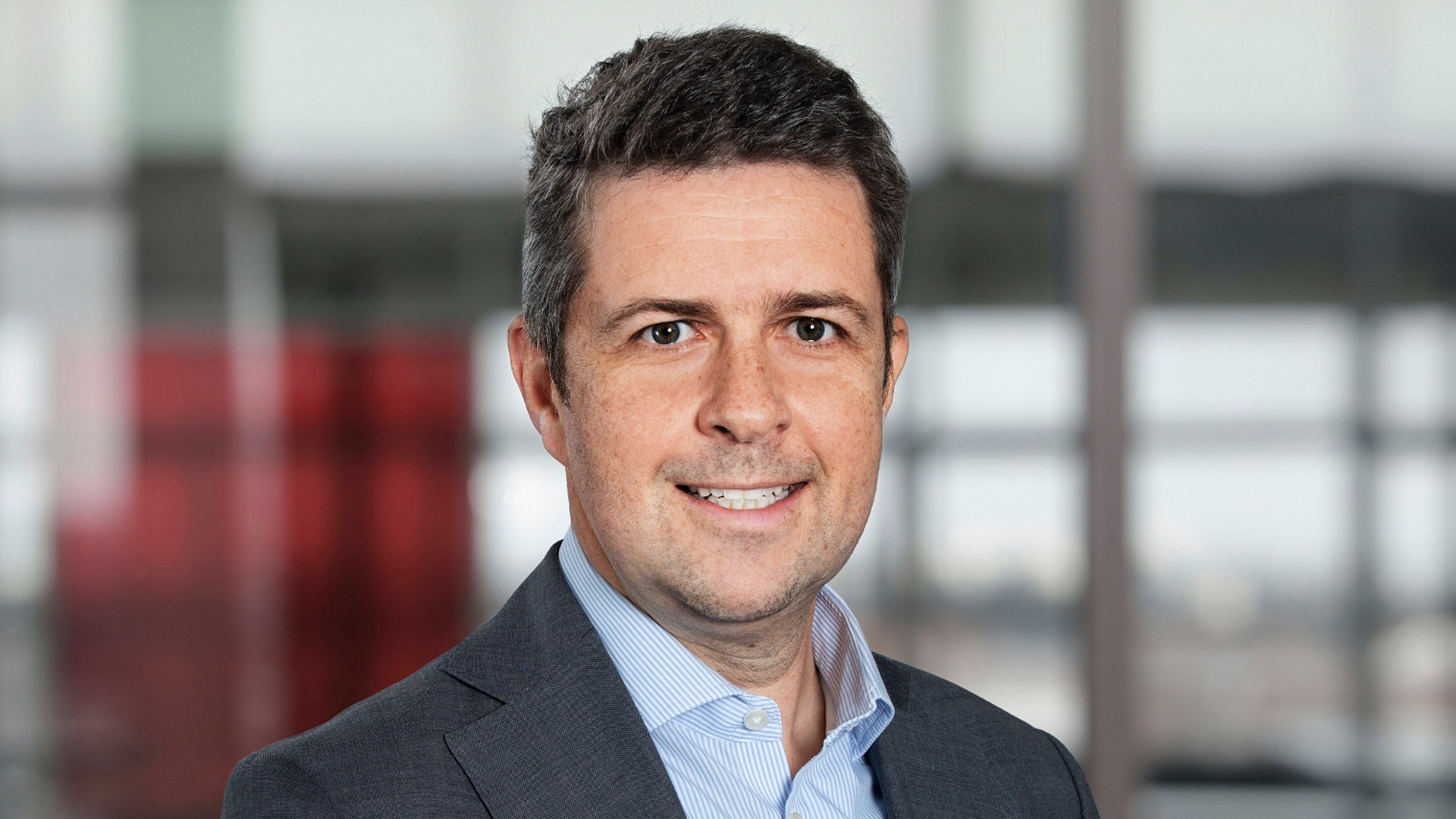
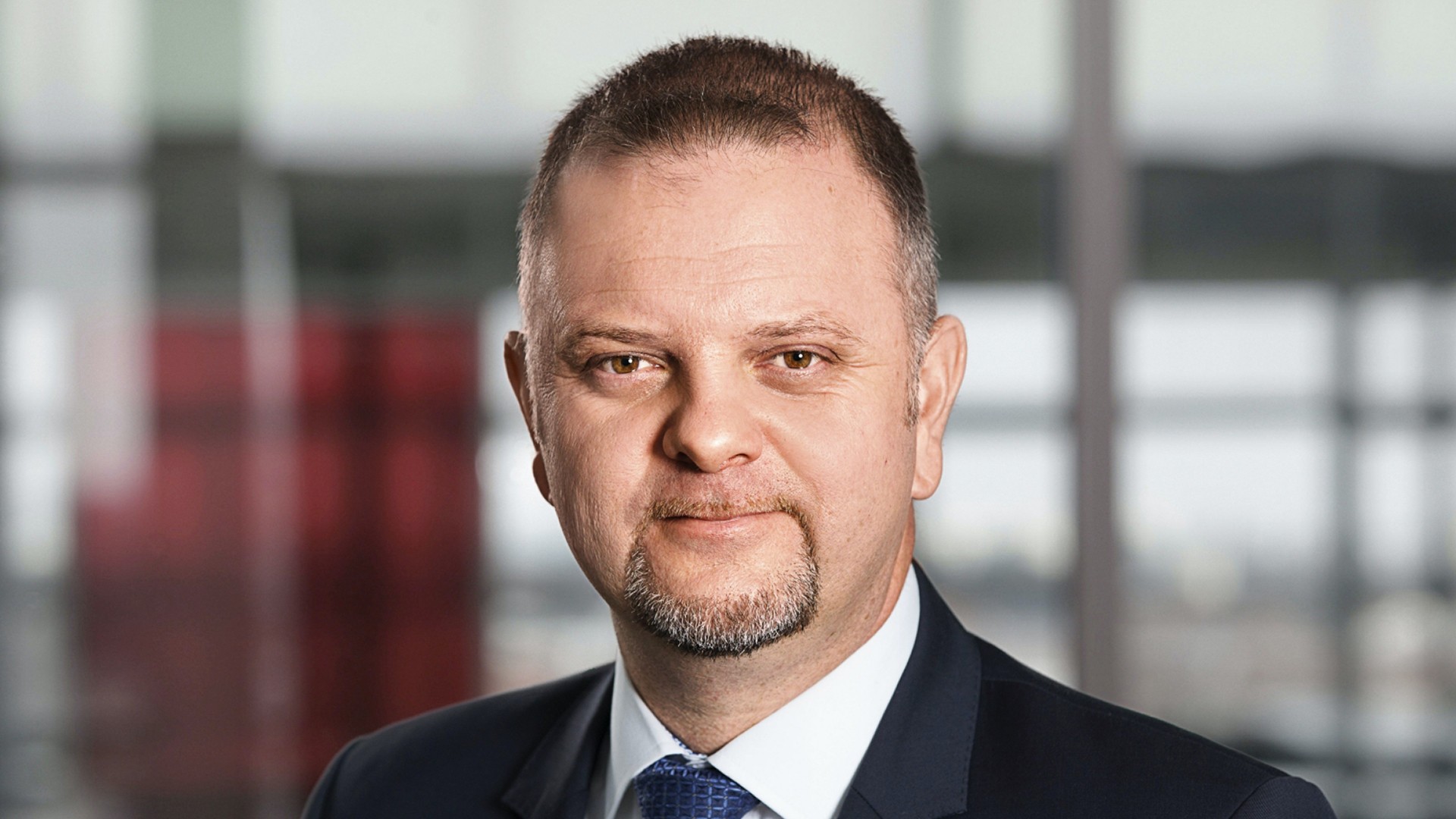
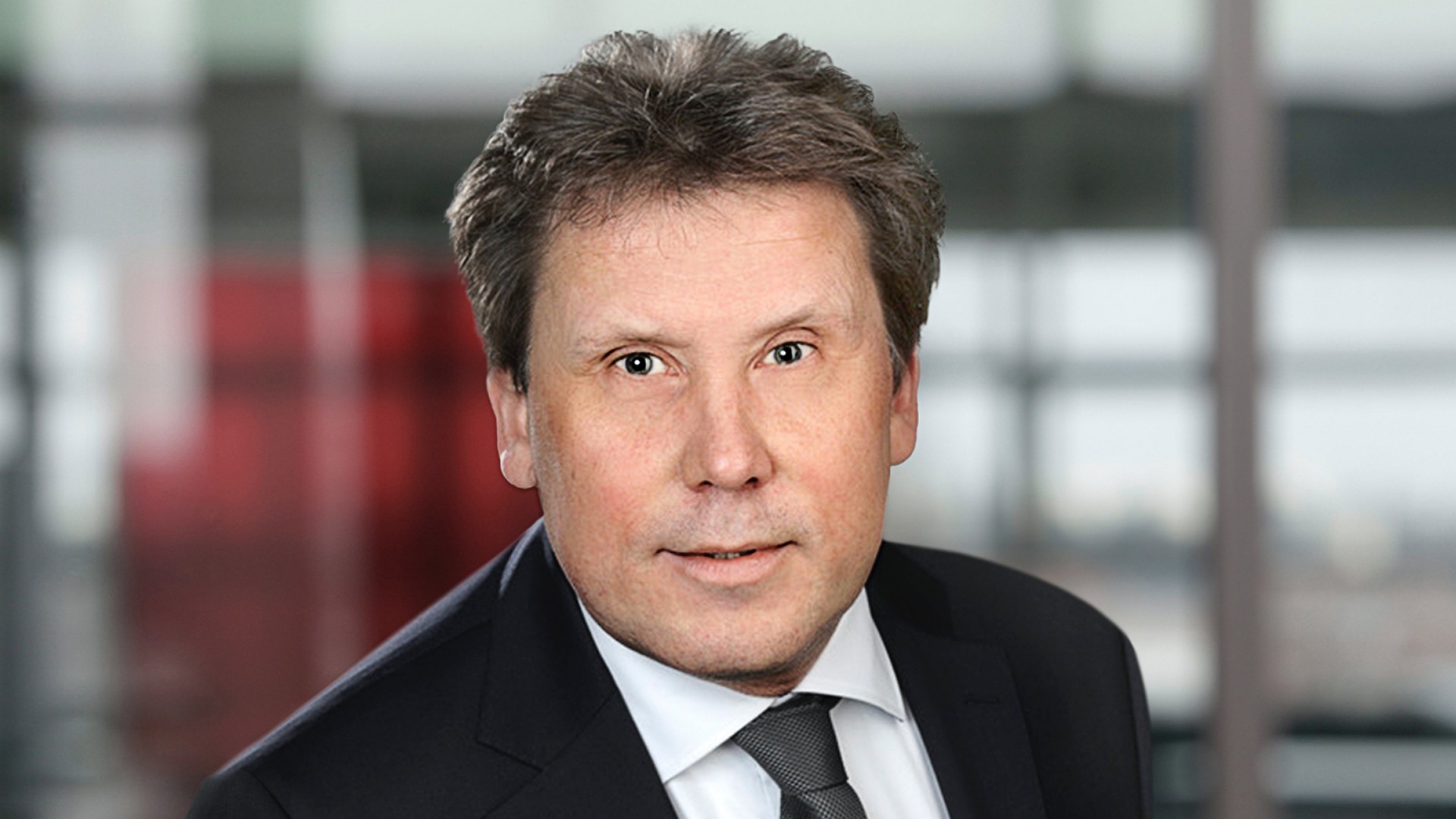