Increasingly, Knorr-Bremse is using innovative “additive manufacturing” technologies in production. In Budapest, Hungary, the company’s experts in advanced 3D metal printing are using the technology to rapidly produce special replacement parts for trains. Their efforts clearly demonstrate the technology’s fascinating potential and the many ways it could be applied to the design of systems for rail transportation.
The future sometimes appears in the most unlikely guises. In the early 1980s, researchers presented a new technology to a highly skeptical public. “Stereolithography” was capable of creating three-dimensional objects using a layering process, in which a laser melted and fused together light-sensitive resins. From a modern viewpoint, the first object they produced appears positively mundane: in 1983, U.S. researcher Chuck Hull “printed” a small, cup-shaped container for performing medical eyewashes – this was the birth of 3D printing. But since those modest beginnings, the technology has advanced from strength to strength.
In recent years, the idea of producing components using “additive manufacturing” techniques has become exponentially more popular as industrial companies continue to digitize their production operations in response to new market expectations. Experts at Knorr-Bremse have been exploring the full potential of this innovative, highly promising technology – and successfully using it in pilot projects for customers.
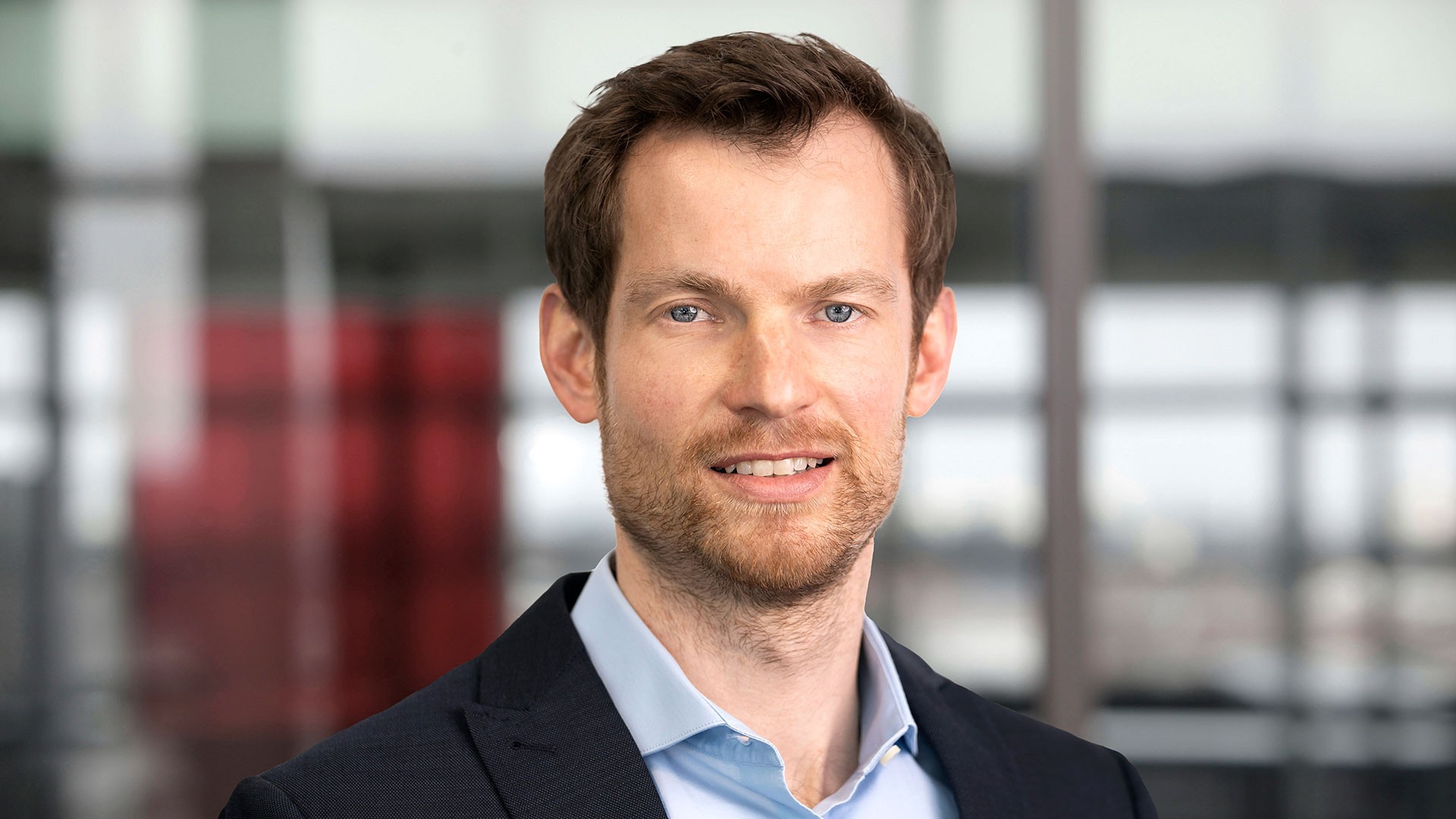
Especially in the rail industry, there’s a growing demand for smaller, lighter components that are also complex and robust. In certain scenarios, additive manufacturing is the ideal technology for this, allowing us to cost-effectively produce special parts even faster and in smaller series than conventional manufacturing techniques.
Bernhard Winkler – Vice President Production Rail, who is also responsible for Digital Manufacturing in Knorr-Bremse’s Rail Vehicle Systems division
“Especially in the rail industry, there’s a growing demand for smaller, lighter components that are also complex and robust,” comments Bernhard Winkler who, as Vice President Production Rail, is also responsible for Digital Manufacturing in Knorr-Bremse’s Rail Vehicle Systems division. “In certain scenarios, additive manufacturing is the ideal technology for this, allowing us to cost-effectively produce special parts even faster and in smaller series than conventional manufacturing techniques.”
Whereas the product costs of conventionally manufactured parts rapidly rise as the components become more complex, Winkler explains that 3D printing is a relatively cost-effective way of reproducing high levels of complexity with intricate details. “The buzzword here is design-driven manufacturing,” he explains, “where design determines the manufacturing process, unfettered by manufacturing constraints, rather than the other way around.” This approach gives designers the freedom to shape a part entirely according to its intended function within the system.
Winkler and a team of 3D printing experts at Knorr-Bremse’s Budapest site were recently confronted by just such a situation in the real world. Colleagues at RailServices – Knorr-Bremse’s aftermarket unit for trains – were unable to cost-effectively procure ten examples of an old replacement part dating back more than 40 years, needed for a longstanding rail service run by a major European operator. The original supplier had long since run out of the tools and jigs required to machine the blanks. So Winkler and his experts turned to additive manufacturing – and used metal printing to successfully recreate the desired parts.
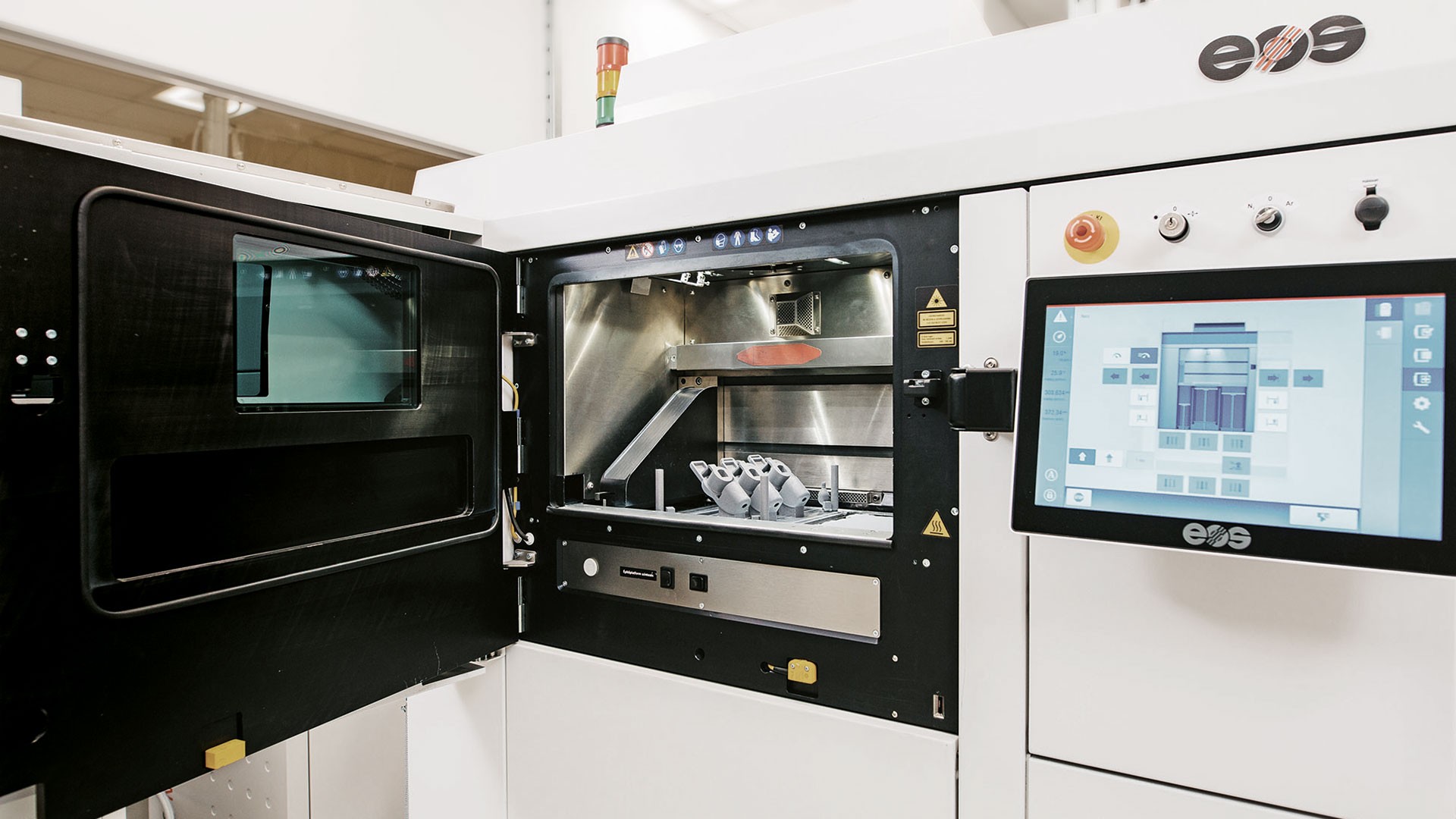
For Winkler, the advantages are obvious. “In mass production – which is still essential – you have to adjust all your machines, tools and jigs to the components you want to manufacture,” he explains. “And while additive manufacturing is still a process that works best in specific scenarios, it’s effectively ready to go as soon as the product data becomes available in the digital process chain.” The printing process itself turns classical manufacturing logic on its head. Rather than milling a metal block until the desired workpiece appears, a special metal powder is fused (or sintered) together by lasers to form the required shape. As a result, the team was able to deliver the components for the RailServices order within a much shorter timeframe than the original 16-week schedule. In short, Knorr-Bremse supplied the parts faster and more cost-efficiently than would have been possible using conventional technology.
Knorr-Bremse now uses 3D printing in a wide variety of applications. For example, the Commercial Vehicle Systems plant in Aldersbach, Bavaria, uses polymer printers to produce prototype components in a matter of hours. “While metal 3D printing as we’re currently using it is an extremely sophisticated process in terms of the technology involved, it’s also an exceptionally promising one,” emphasizes Winkler. While 3D printing is ideal for producing prototypes for development, as well as tools and molds, using it to manufacture small series of spare parts takes the whole process to a higher level. Advanced design is, however, regarded as the “ultimate discipline”, offering product designers a whole new level of freedom and providing automakers with the cost-efficient flexibility to build more highly integrated vehicles that weigh less. This is also why advanced design plays such an important role in, for example, aircraft construction. And once again, the Budapest team has already demonstrated the technology’s potential in this field.
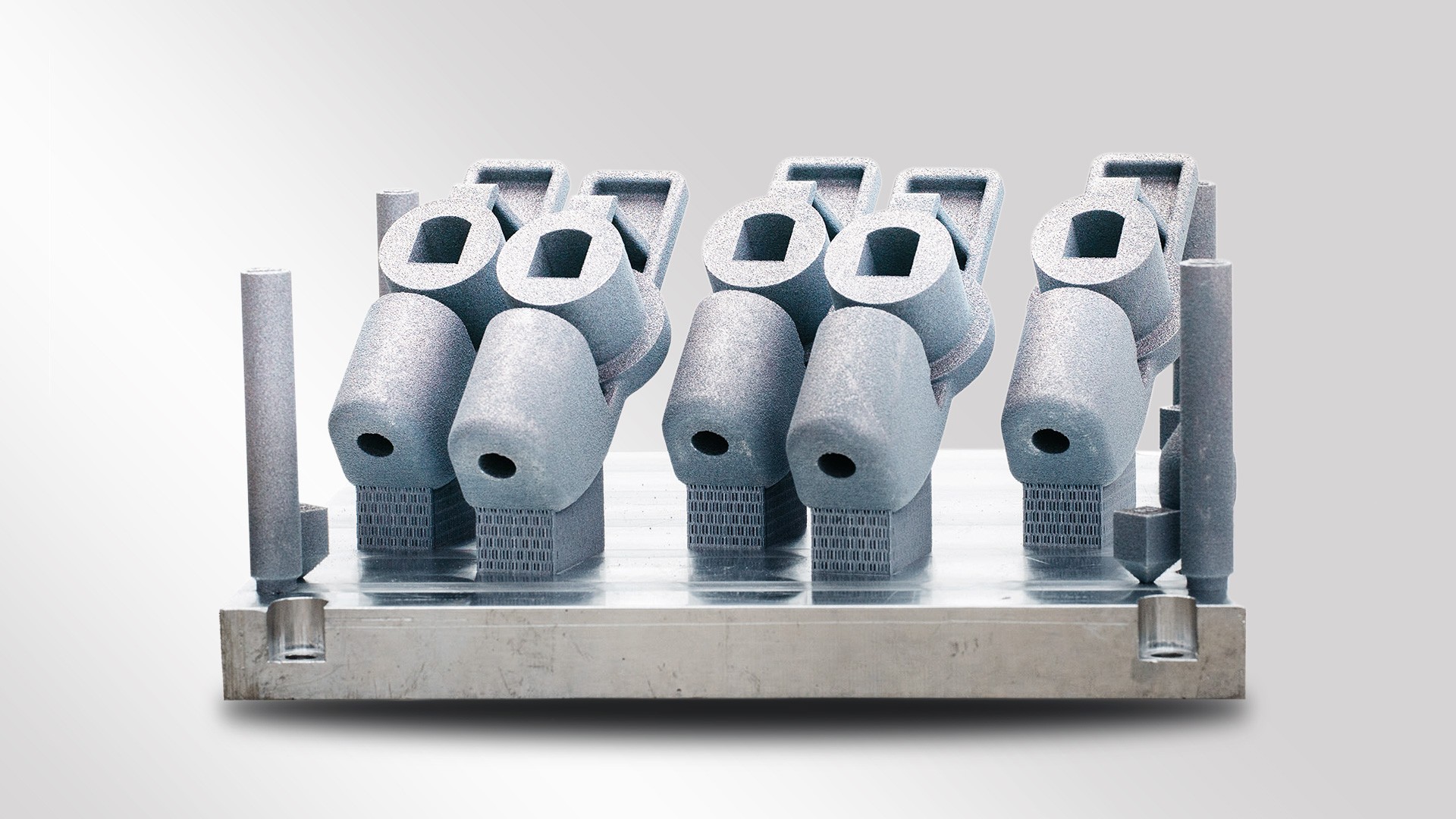
Making braking-system components up to 90 percent lighter
As part of a wide-ranging 3D printing feasibility study, a cross-divisional, multi-site team designed a significantly lighter and more compact control panel for sanding systems. Part of a train’s braking system, the job of a sanding system is to selectively spray sand onto wheel-rail contact points whenever adhesion is low – due to wet rails, for example – thereby ensuring that braking forces are applied more effectively. “The functionality tests we performed on the new component showed almost exactly the same performance figures as a conventionally manufactured panel, and yet the part is over 90 percent lighter,” reveals Dr. Attila Kovács, Director Mechanical Design Engineering at Knorr-Bremse’s Budapest plant. Use-case scenarios include low-floor vehicles or future high-speed trains with restricted installation space.
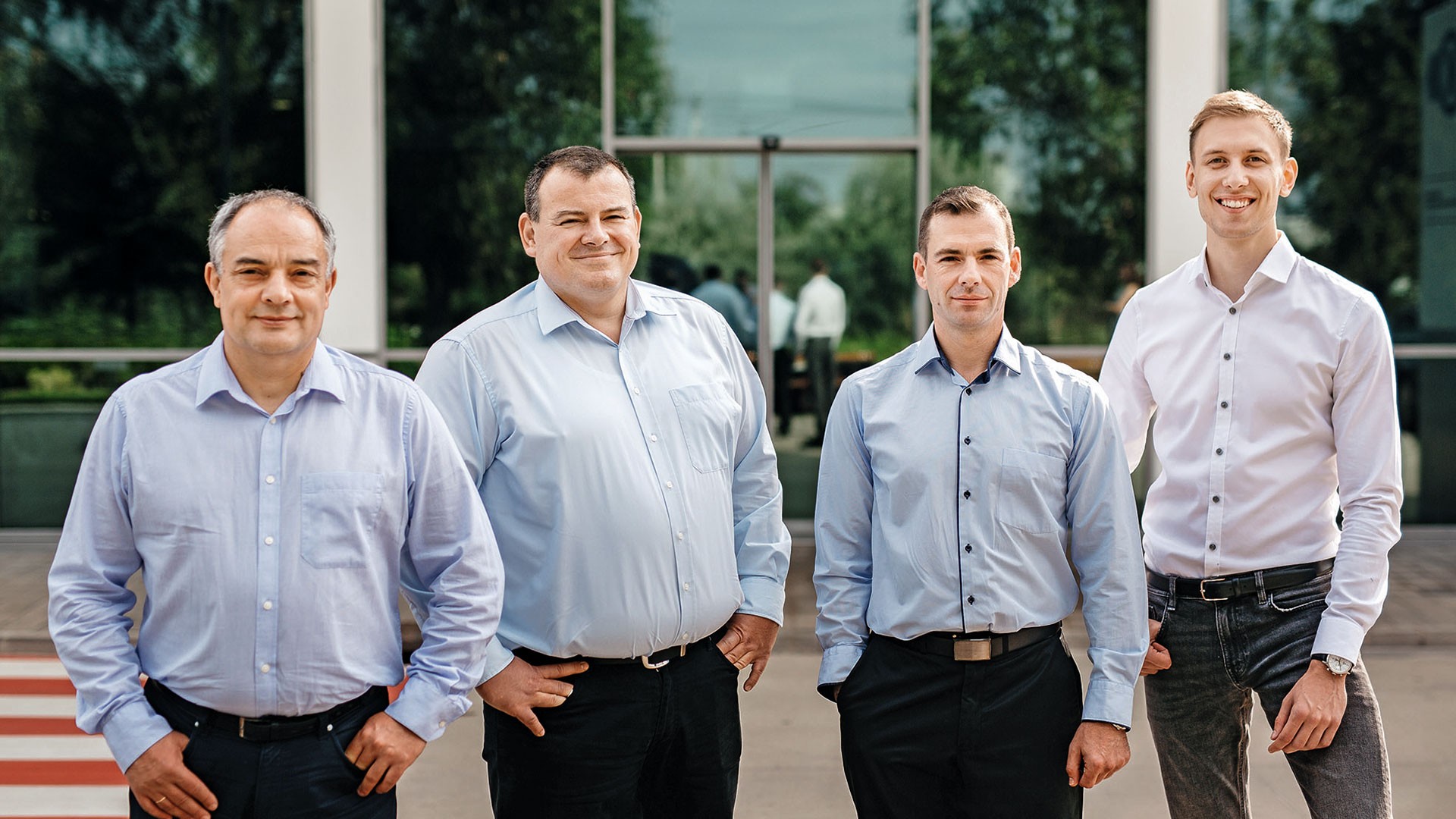
Earlier this year, the team of experts even succeeded in obtaining official certification for the metal 3D printing process. This represents a major step forward for applications involving additively manufactured components for rail vehicles, confirms Kovács. This is because the output of a metal 3D printing process is influenced by around 170 different parameters. Some of them are easy to control, such as the temperature or pressure in the build chamber. But others are highly interdependent, which means performing countless series of tests. “That’s precisely why we need process certification, so we can put these 3D-printed parts into circulation,” adds Winkler. “The German Federal Rail Authority requires comprehensive quality management, and our customers also need proof that the printer consistently produces stable, reliable results. Ultimately, we must meet the same standards as we do in conventional manufacturing.”
Based on this successful process certification, Knorr-Bremse was able to guarantee the availability of the 3D-printed replacement part for the RailServices maintenance project (the original part dates back to 1947), setting a milestone in the supply of replacement parts manufactured using additive technology. The rail operator was delighted by the demonstrably high technical standard achieved by the final result, and now other customers in the metro sector are showing interest in buying additively manufactured components “made by Knorr-Bremse” – as is a major national rail operator. The 3D printing team is looking forward to tackling new challenges: “Now that our Budapest facility is fully operational, we’re looking forward to supporting other customers in mission-critical situations and contributing to the stability of their businesses by helping to safeguard rail vehicle uptime.”
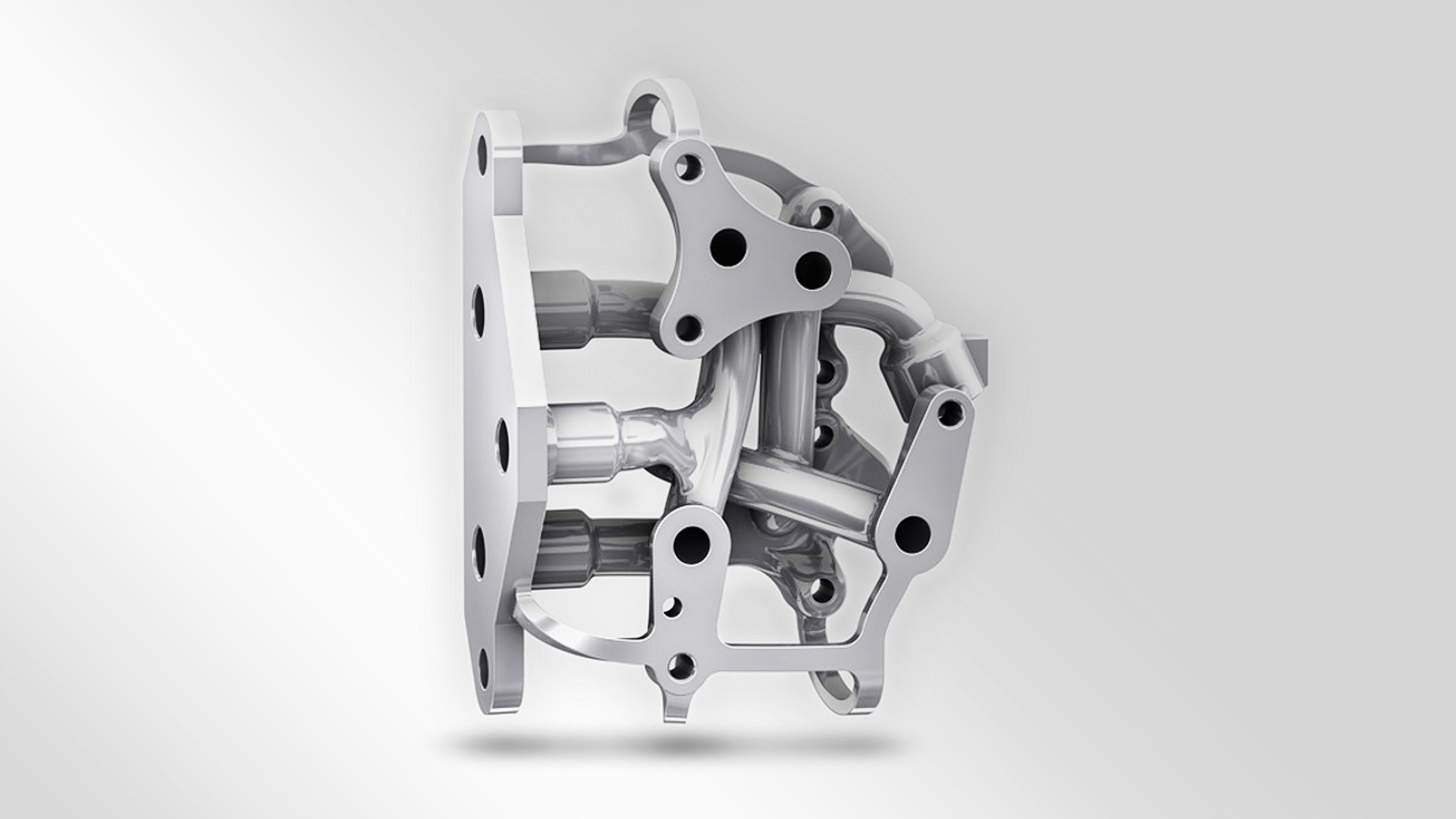