Innovative Technologien zur „additiven Fertigung“ finden in der Produktion bei Knorr-Bremse immer breitere Anwendung. Die Experten für anspruchsvollen 3D-Metalldruck in Budapest ermöglichen so nicht nur schnelle Lösungen für spezielle Ersatzteile für Züge, sondern zeigen das faszinierende Potenzial der Technologie und seine zahlreichen Möglichkeiten in der Konstruktion von Systemen für den Schienenverkehr auf.
Zukunft nimmt manchmal die unscheinbarsten Formen an. Anfang der 1980er präsentierten Forscher einer skeptischen Öffentlichkeit eine Technik, die es erlaubte, Gegenstände durch ein Schichtverfahren herzustellen, indem ein Laser lichtempfindliche Harze miteinander verschmolz. Das erste per „Stereolithografie“ hergestellte Objekt mutet heute profan an: 1983 „druckte“ der Amerikaner Chuck Hull einen kleinen Becher, mit dem sich medizinische Augenspülungen durchführen ließen. Der 3D-Druck war geboren. Seine Entwicklung lässt sich als Siegeszug betiteln.
Nicht zuletzt hat der Ansatz, Komponenten mittels „additiver Fertigung“ herzustellen, gerade in den letzten Jahren im Zuge der zunehmend digitalen Produktion bei Industrieunternehmen und neuen Marktanforderungen eine weitere Dimension erlangt. Auch Experten bei Knorr-Bremse haben das Potenzial der innovativen und vielversprechenden Technologie untersucht – und in Pilotprojekten für Kunden erfolgreich zur Anwendung gebracht.
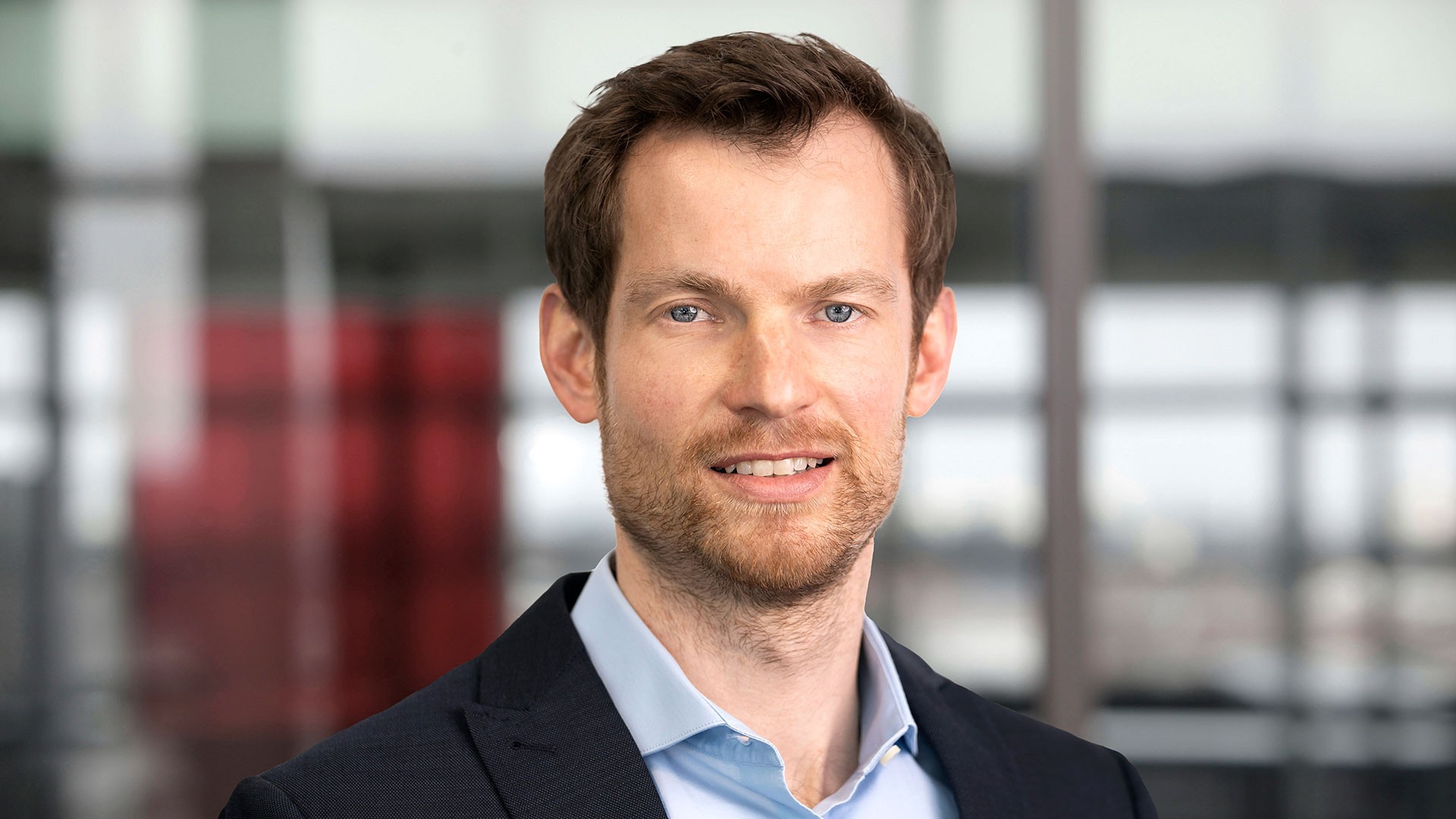
Gerade die Bahnindustrie verlangt zunehmend nach kleineren und leichteren, aber dennoch komplexen und robusten Komponenten. Additive Fertigung bietet dafür in besonderen Szenarien eine geeignete Technologie, da wir spezielle Teile im Vergleich zur herkömmlichen Fertigung noch schneller und in kleineren Stückzahlen wirtschaftlich produzieren können.
Bernhard Winkler – Bereichsleiter Production Rail, u. a. verantwortlich für Digital Manufacturing bei der Knorr-Bremse Division Systeme für Schienenfahrzeuge
„Gerade die Bahnindustrie verlangt zunehmend nach kleineren und leichteren, aber dennoch komplexen und robusten Komponenten“, sagt Bernhard Winkler, als Bereichsleiter Production Rail u.a. verantwortlich für Digital Manufacturing bei der Knorr-Bremse Division Systeme für Schienenfahrzeuge. „Additive Fertigung bietet dafür in besonderen Szenarien eine geeignete Technologie, da wir spezielle Teile im Vergleich zur herkömmlichen Fertigung noch schneller und in kleineren Stückzahlen wirtschaftlich produzieren können.“
Während bei konventionell hergestellten Teilen die Produktkosten mit der Komplexität ansteigen, erlaube der 3D-Druck, hohe Komplexitäten und filigrane Details vergleichsweise günstig abzubilden. „Design-driven Manufacturing ist das Stichwort, bei dem die Konstruktion die Fertigung bestimmt und nicht mehr die Fertigung die Konstruktion“, sagt Winkler. Der Ansatz eröffnet die Freiheit, die Gestaltung eines Teils ganz nach dessen Funktion im System umzusetzen.
Konkret waren Winkler und ein Team aus 3D-Druck-Experten vom Knorr-Bremse Standort in Budapest mit einer solchen Situation konfrontiert, als die Kollegen von RailServices – der Nachmarkteinheit von Knorr-Bremse für Züge – für eine dienstältere Bahn eines großen europäischen Betreibers zehn Stück eines über 40 Jahre alten Ersatzteils nicht wirtschaftlich beschaffen konnten. Der bisherige Lieferant hatte längst keine Werkzeuge und Vorrichtungen mehr für die Rohteile. Winkler und die Experten setzten auf das additive Verfahren – und konnten die gewünschten Teile per Metalldruck herstellen.
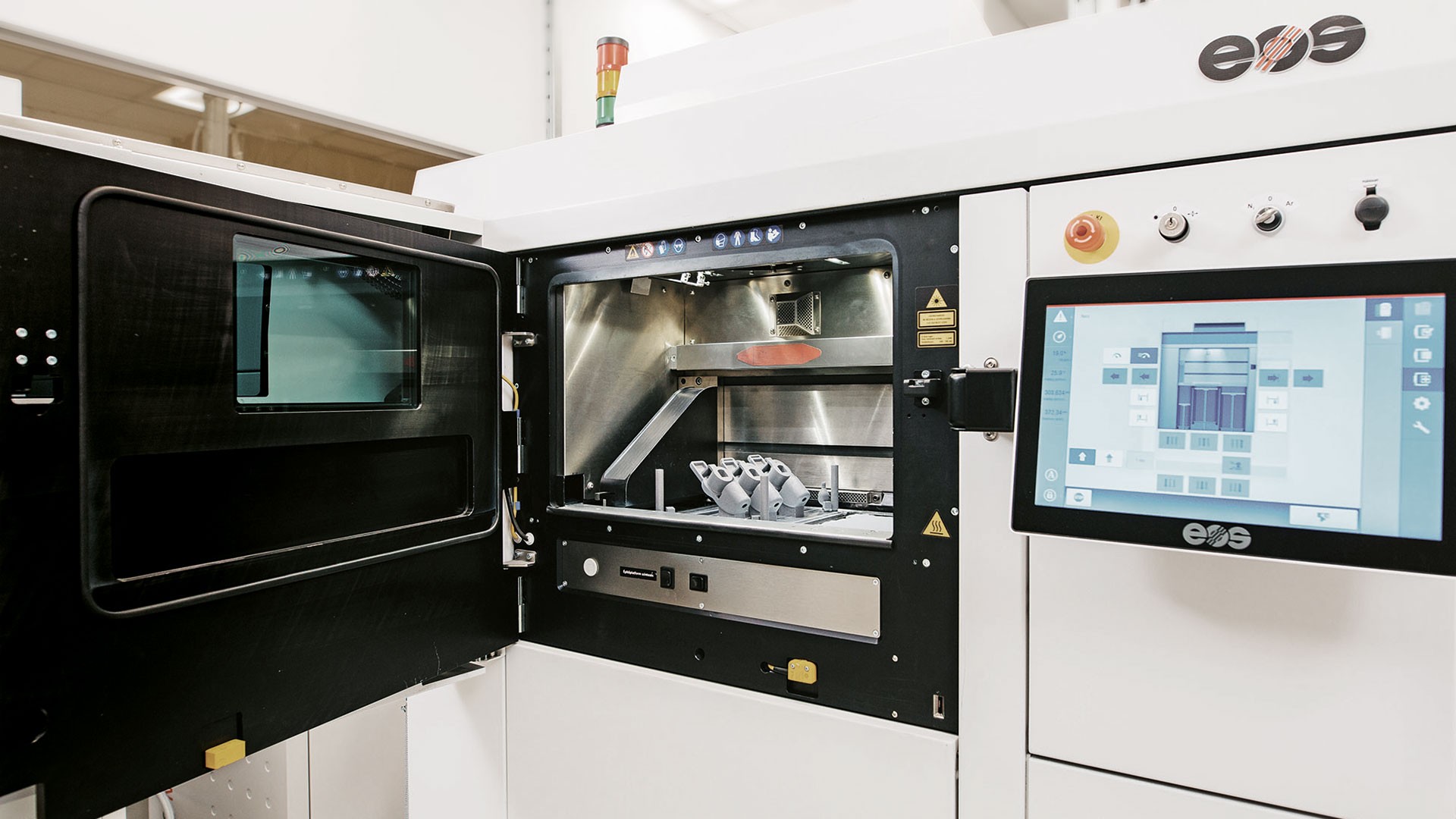
Für Winkler liegen die Vorteile auf der Hand: „In der Massenproduktion, die unerlässlich bleibt, müssen Maschinen, Werkzeuge und Vorrichtungen auf die zu fertigenden Komponenten eingestellt werden“, sagt er. „Die additive Fertigung ist zwar ein Verfahren für Sonderszenarien, dafür sind wir aber gleich startklar, sobald die Produktdaten in der digitalen Prozesskette verfügbar sind.“ Der Druckprozess selbst kehrt die klassische Herstellungslogik um: Es wird nicht ein Metallblock so bearbeitet, dass dabei ein gewünschtes Teil entsteht, sondern ein spezielles Metallpulver per Laser so zusammengefügt, dass es Gestalt annimmt. Die Komponenten für den RailServices Auftrag konnten so deutlich kurzfristiger als in den ursprünglich geplanten 16 Wochen geliefert werden. Knorr-Bremse konnte schneller und kostengünstiger liefern als mit konventioneller Technologie.
Insgesamt gibt es bei Knorr-Bremse mittlerweile ein breites Anwendungsfeld für den 3D-Druck. So nutzt etwa das Werk für Systeme für Nutzfahrzeuge im bayerischen Aldersbach Kunststoffdrucker, um innerhalb weniger Stunden Prototypen-Bauteile herzustellen. „Gerade der Metall-3D-Druck, wie wir ihn zur Anwendung bringen, ist jedoch ein technologisch extrem anspruchsvolles, dafür aber auch äußerst vielversprechendes Verfahren“, sagt Winkler. Während es mittels 3D-Druck möglich ist, Prototypen für die Entwicklung sowie Werkzeuge und Gussformen zu drucken, ist die Fertigung von Ersatzteilen in kleinen Stückzahlen schon eine höhere Kunst. Als „Königsdisziplin“ gilt jedoch das „Advanced Design“: Es ermöglicht nochmals neue Freiheitsgrade in der Produktgestaltung und unterstützt Fahrzeugbauer bei der flexiblen, kosteneffizienten Fahrzeugintegration sowie der Reduktion von Gewicht. Auch deshalb spielt Advanced Design etwa im Flugzeugbau eine wichtige Rolle. Auch auf diesem Feld zeigte das Budapester Team die Potenziale der Technologie auf.
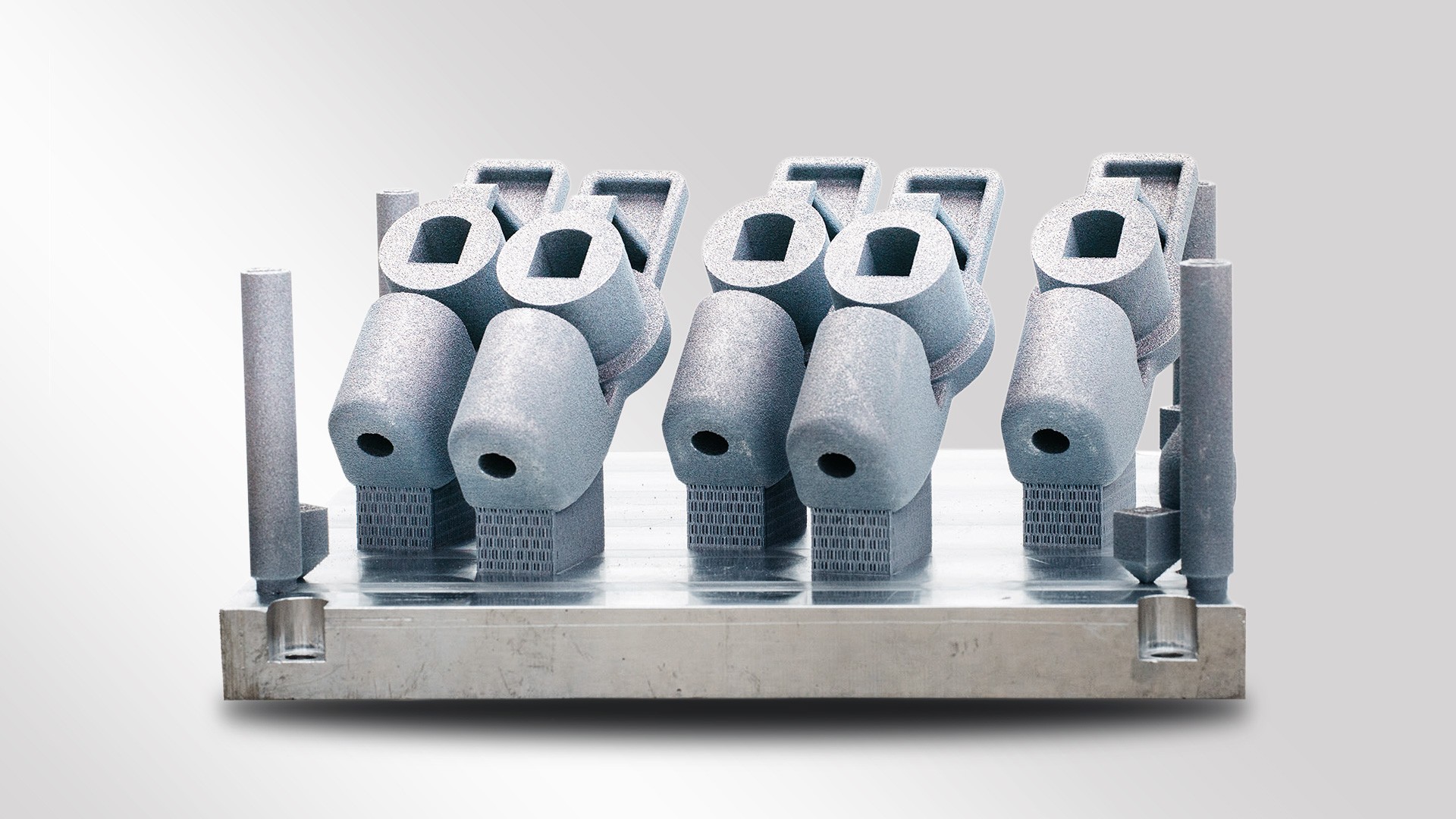
Komponenten für Bremssysteme: Bis zu 90 Prozent leichter
Im Rahmen einer breit angelegten 3D-Druck-Machbarkeitsstudie konstruierte ein bereichs- und standortübergreifendes Team eine deutlich leichtere und kompaktere Steuerungstafel für Sandungssysteme. Diese sind Teil der Bremssysteme von Zügen und haben die Aufgabe, bei niedrigem Kraftschluss – etwa durch nasse Schienen – gezielt Sand in den Rad-Schienen-Kontakt zu sprühen, um für eine bessere Übertragung der Bremskräfte zu sorgen. „Die mit dem neuen Bauteil durchgeführten Funktionstests ergaben im Vergleich zu konventionell produzierten Tafeln zwar nahezu deckungsgleiche Werte, doch ist das Teil über 90 Prozent leichter“, berichtet Dr. Attila Kovács, Director Engineering im Budapester Knorr-Bremse Werk. Als Einsatzszenarien seien die engen Einbauräume in Niederflurfahrzeugen oder in zukünftigen Hochgeschwindigkeitszügen denkbar.
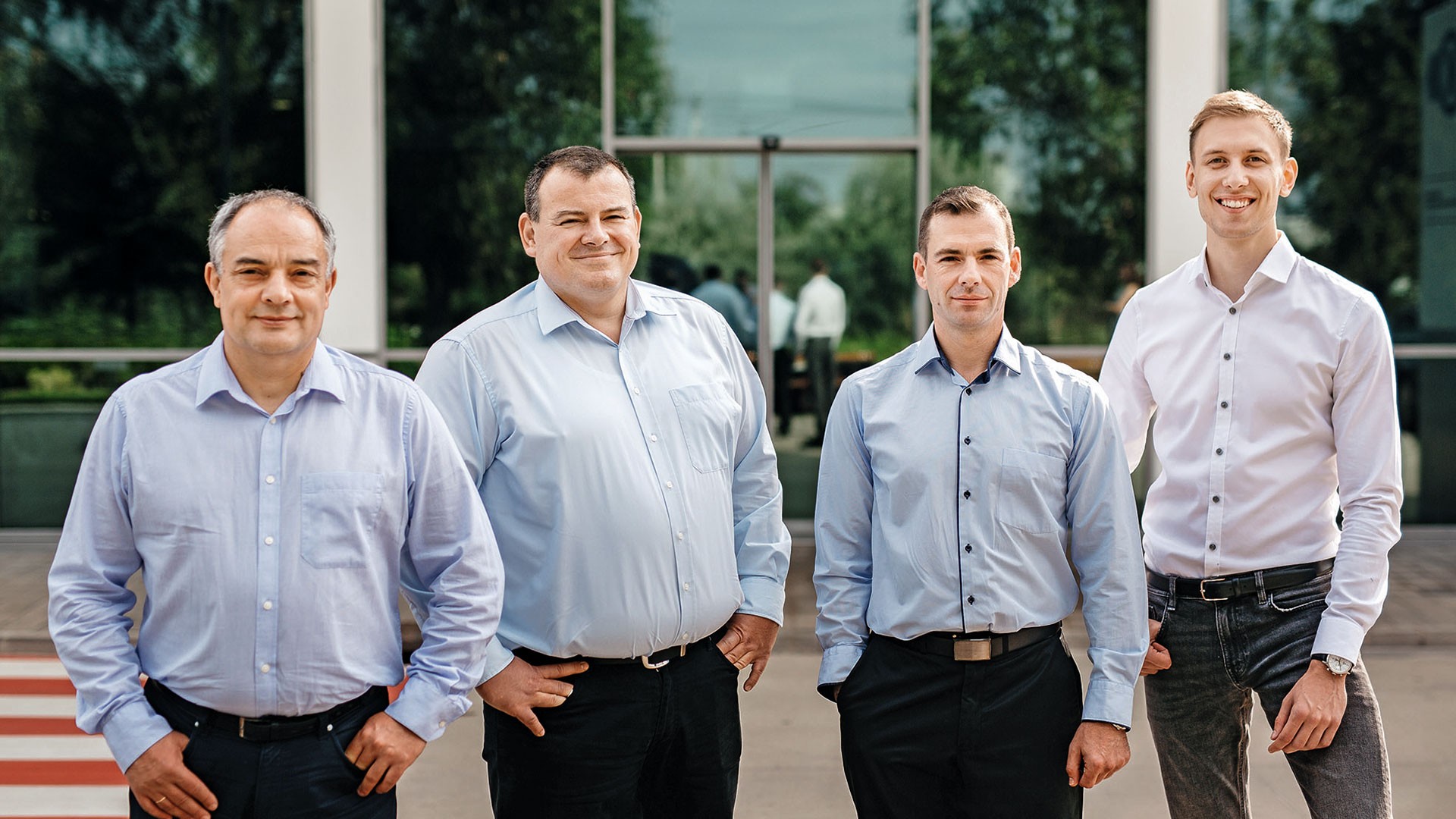
Den Metall-3D-Druckprozess konnte das Experten-Team Anfang des Jahres sogar offiziell qualifizieren. Damit wurde ein großer Schritt zum Einsatz von additiv gefertigten Bauteilen in Schienenfahrzeugen erfolgreich erreicht, wie Kovács berichtet. Denn: Rund 170 Parameter beeinflussen das Ergebnis des Metall-3D-Druckprozesses. Einige seien leicht zu steuern, wie Temperatur oder Druck in der Kammer. Andere hingen stark voneinander ab, weswegen oft unzählige Testreihen notwendig seien. „Gerade deswegen brauchen wir die Prozessqualifizierung, um die Bauteile in den Verkehr zu bringen“, ergänzt Winkler. „Das Eisenbahnbundesamt verlangt ein umfangreiches Qualitätsmanagement, und auch unsere Kunden fordern den Nachweis, dass stabile und zuverlässige Ergebnisse aus dem Drucker kommen. Letztlich gelten die gleichen Anforderungen wie in der konventionellen Fertigung.“
Auf Basis der erfolgreichen Prozessqualifizierung gelang es auch im Rahmen des Wartungsprojekts von RailServices, die Verfügbarkeit des Ersatzteils, dessen Erstausführung aus dem Jahr 1947 stammt, sicherzustellen und damit bei der Auslieferung additiv hergestellter Ersatzteile einen Meilenstein zu setzen. Während sich der Bahnbetreiber sehr erfreut über den nachgewiesenen hohen technischen Standard äußerte, haben inzwischen weitere Kunden aus dem Metrobereich sowie ein weiterer nationaler Bahnbetreiber ihr Interesse an additiv gefertigten Bauteilen „made by Knorr-Bremse“ bekundet. Das 3D-Druck-Team ist gespannt auf neue Aufgaben: „Nachdem die Anlage in Budapest nun vollumfänglich einsatzbereit ist, freuen wir uns darauf, weiteren Kunden in erfolgskritischen Situationen zur Seite zu stehen, so einen Beitrag zur Stabilität ihres Betriebs zu leisten und dabei zu helfen, verfügbare Mobilität auf der Schiene abzusichern.“
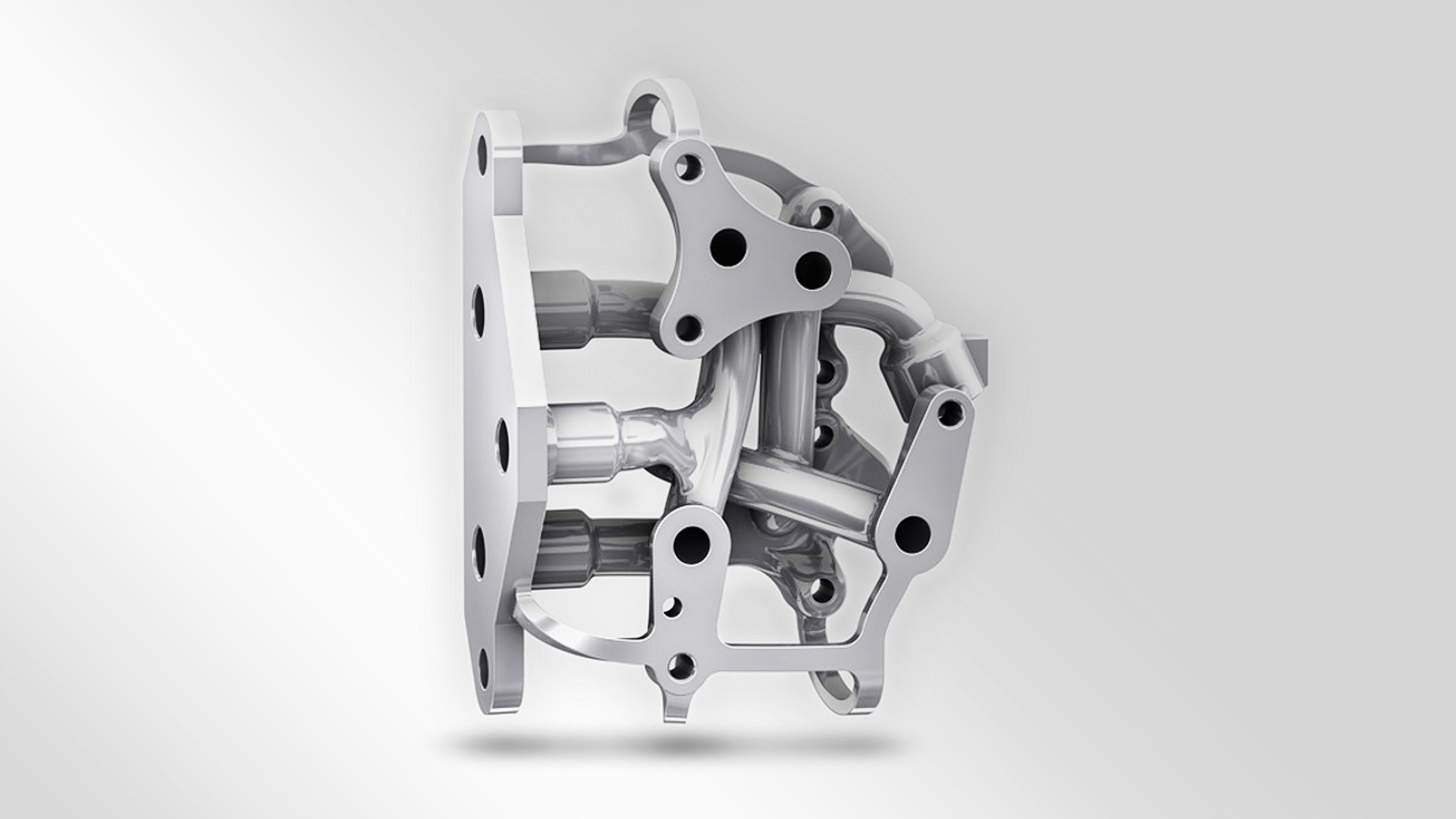